This plan maintain stable machine capacity and workforce levels with constant output rate • In simple level strategy seeks to produce an aggregate plan that maintains a steady production rate and/or a steady employment level • This plan is preferable to the industry where non perishable materials are processed, but not immediately soldWith a beginning annual inventory of 600 and an ending annual inventory of 600, which set of values are correct for a Level Capacity aggregate planning strategy within Solution andAbout Press Copyright Contact us Creators Advertise Developers Terms Privacy Policy & Safety How works Test new features Press Copyright Contact us Creators
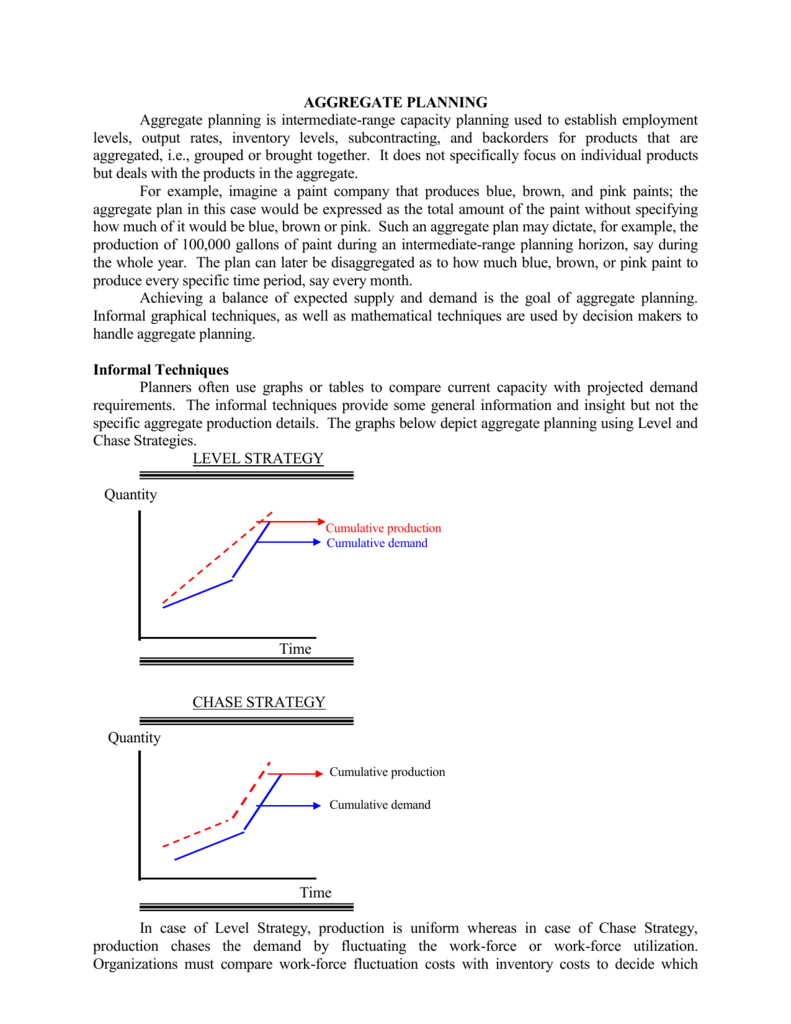
Aggregate Planning
What are the aggregate planning strategies
What are the aggregate planning strategies- 6 types of aggregate planning strategies At a basic level, you have two options you can modify demand to meet your production capacity, or you can modify capacity to The reactive aggregate planning strategy creates changes in the capacity to match with the changing demand Here are options widely used when developing the reactive aggregate planning strategy Resource Management Companies change resource management policies by hiring employees with required skills and lay off those without the right skills




Slides Show
What strategies are used for aggregate planning and what are the main differences between these strategies? Level Production Strategy Level production = 100,000 pounds (50,000 1,000 150,000 80,000) 4 Spring 80,000 100,000 ,000 Summer 50,000 100,000 70,000 Fall 1,000 100,000 50,000 Winter 150,000 100,000 0 400,000 140,000 Cost of Level Production Strategy (400,000 X $0) (140,00 X $50) = $870,000 SALES PRODUCTION QUARTER FORECAST PLAN A level strategy's main goal is to create an aggregate plan that keeps both production and employment steady This means that the organization needs to come up with other ways of addressing changes in customer demand, like modifying their inventory levels based on how demand is forecasted to evolve in the near future
Regular time output = Minimum(Forecast, Capacity) Level Required production = Average forecasted demand per period Number of workers = (Required Production/period) / (Production rate/ worker/period) Chapter 12 Material Requirements Planning GR Plannedorder releases of "parents" x No required per unit OR Master Schedule for level zero Aggregate Planning and Forecasting Aggregate Planning by definition is concerned with determining the quantity and scheduling of production for the midterm future The timing on an aggregate plan runs normally from 3 to 18 months Therefore, the plan is a byproduct of the longer term strategic plan This is an important differentiation sinceA level strategy seeks to produce an aggregate plan that maintains a steady production rate and/or a steady employment level In order to satisfy changes in customer demand, the firm must raise or lower inventory levels in anticipation of increased or decreased levels of forecast demand
Aggregate Planning Strategies Capacity Options Aggregate Planning Strategies 1 Use inventories to absorb changes in demand 2 Accommodate changes by varying workforce size 3 Use parttimers, overtime, or idle time to Develop a Plan Level strategy Aggregate planning is an operational activity critical to the organization as it looks to balance longterm strategic planning with short term production success A complete information is required about available production facility and raw materials A solid demand forecast covering the mediumrange periodAggregate production planning (APP) determines the resource capacity a firm will need to meet its demand over an intermediate time horizonsix to twelve months in the future Within this time frame, it is usually not feasible to increase capacity by building new facilities or purchasing new equipment;



Strategies For Developing Aggregate Plans Assignment Help Aggregate Planning Process
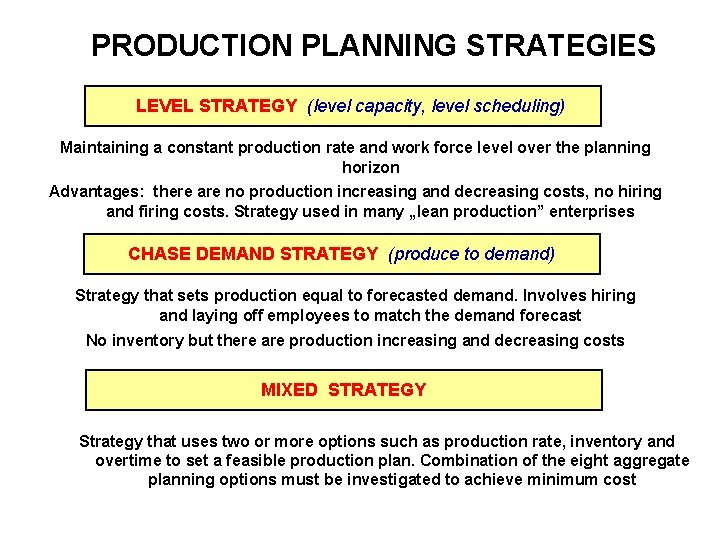



Sales And Operations Planning Aggregate Planning Production Planning
7 Level Strategy • Level strategy is a strategy the firm maintains a constant capacity over a period of time irrespective of the fluctuations in demand • This strategy is used when the skill level, training required, or the cost of hiring people and terminating them is high Demand Units Time Production 7Aggregate planning – Is the process by which a company determines levels of capacity, production, subcontracting, inventory, stockouts, and pricing over a specified time horizon – goal is to maximize profit Or, if demand is effectively fixedThe primary difference among the three strategies is the lever, When an organization adopts the level capacity strategy then it manufactures at a constant output rate It does not consider any fluctuation or change in the level of demand
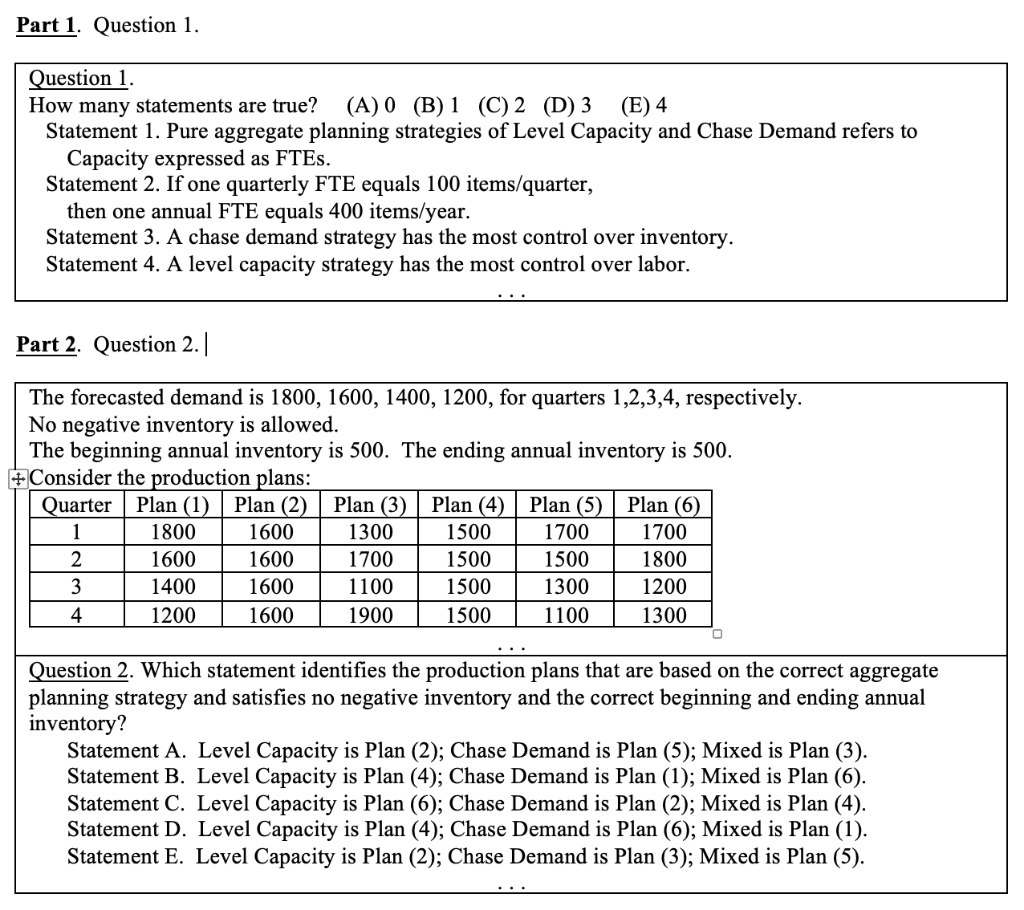



Part 1 Question 1 Question 1 How Many Statements Chegg Com
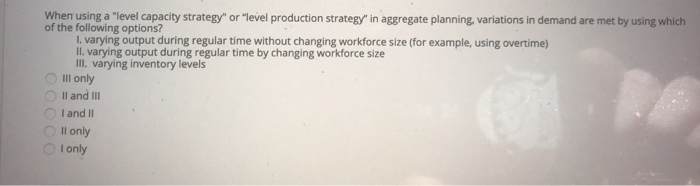



Solved When Using A Level Capacity Strategy Or Level P Chegg Com
In this lesson, we investigate the process of developing a level production plan in this aggregate planning segmentThe three pure aggregate planning strategies are the chase strategy, time flexibility from workforce or capacity strategy, and the level strategy The primary difference among the three strategies is the lever, that is, the parameter that is manipulated to achieve equality of supply and demand over the aggregate planning periodStrategic Network Planning Master Planning Distribution Planning Transport Planning Production Aggregate Planning a Level Work Force Plan `backorders allowed Aggregate Planning Available capacity 50 50 10 12 14 16 0 350 150 50 75 75 0 300 300
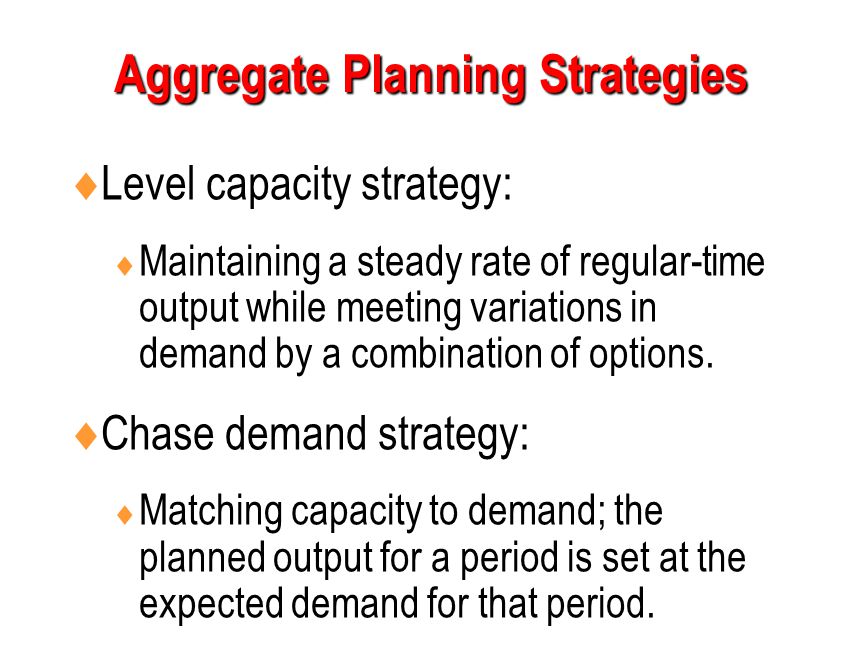



Aggregate Planning Ppt Download
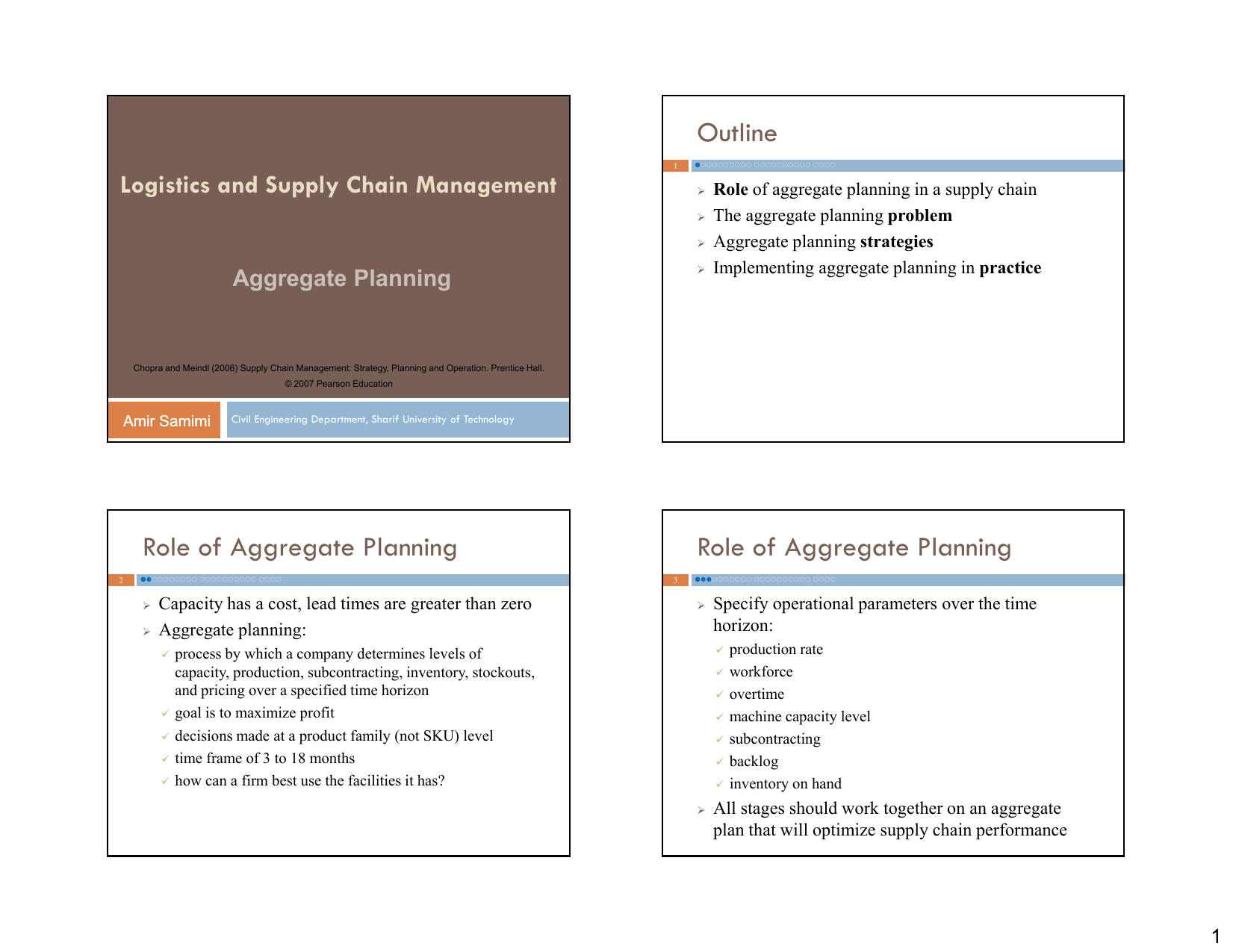



08
1 Level Strategy The level strategy favors an aggregate plan that maintains a more steady production and steady employment levels To accommodate the changes in customer demand, organizations must either increase or decrease inventory The level strategy is considered a traditional aggregate planning method that maintains a steady production rate as well as the level of the workforce by continuing consistent human resources and production in the organization It is best suited where the inventory carrying costs are not high and are adopted by mainly manufacturing companies 1 For next fiscal year, find their annual regular time direct labor cost and their overtime direct labor cost based on a level capacity aggregate planning strategy 2 For next fiscal year, find their annual regular time direct labor cost and their overtime direct labor cost based on a chase demand aggregate planning strategy




Aggregate Capacity Planning Pdf Free Download



Http Www1 Pu Edu Tw Ylai Erp Dom 1042 Ppts S16 1042 Erp Dom Ap S16 Pdf
Aggregate planning is capacity planning for a the long range b the intermediate range c the short range d typically one to three months e typically one or more years B The main disadvantage (s) of informal techniques used for aggregate planning is (are) aDisaggregating the Aggregate Plan Aggregate Planning Aggregate planning Intermediaterange capacity planning that typically covers a time horizon of 2 to 18 months Useful for organizations that experience seasonal, or other variations in demand Goal Achieve a production plan that will effectively utilize the organizations' resources to satisfy demand Sales and Operations Planning Some organizations use the term sales operations and planning rather than aggregate planningAn approach to aggregate planning that attempts to match supply and output with fluctuating demand Depending on the product or service involved, the approach can incur costs by the ineffective use of capacity at periods of low demand, by the need to recruit or lay off staff, by learningcurve effects, and by a possible loss of quality The advantages include low storage
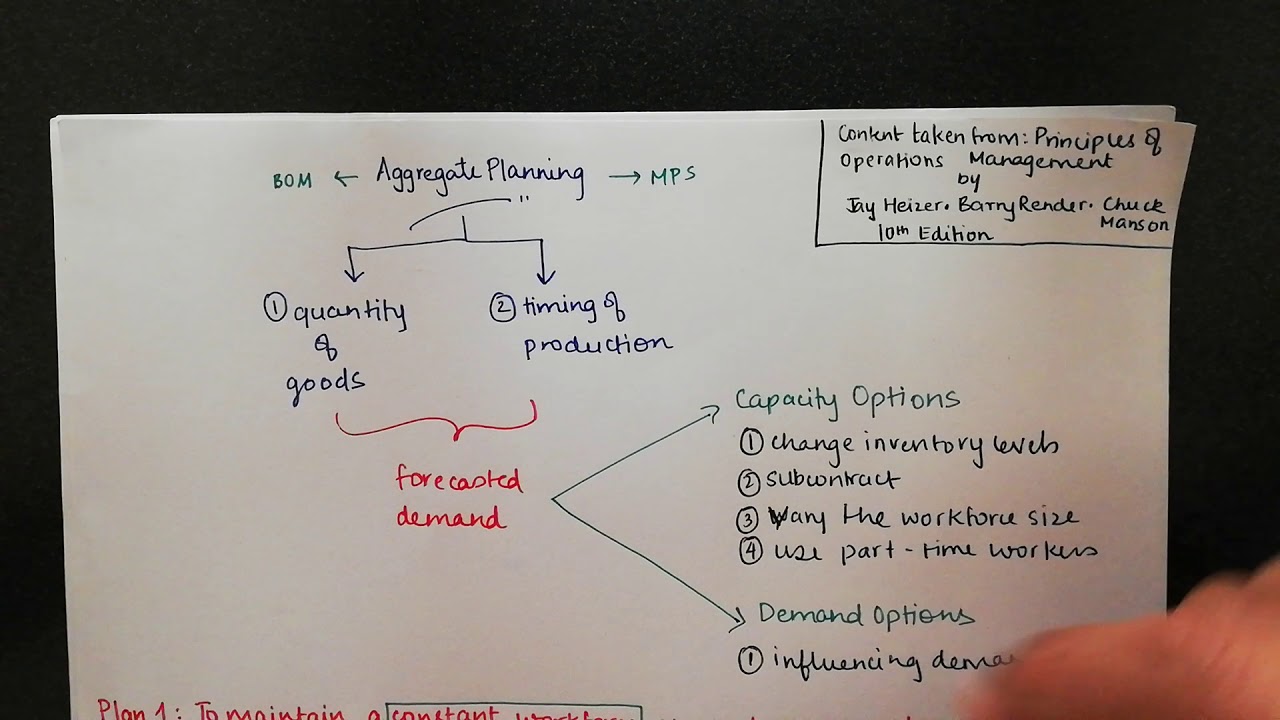



Case Study Red Tomato Aggregate Plan Part 1 By Fpt Technology Official
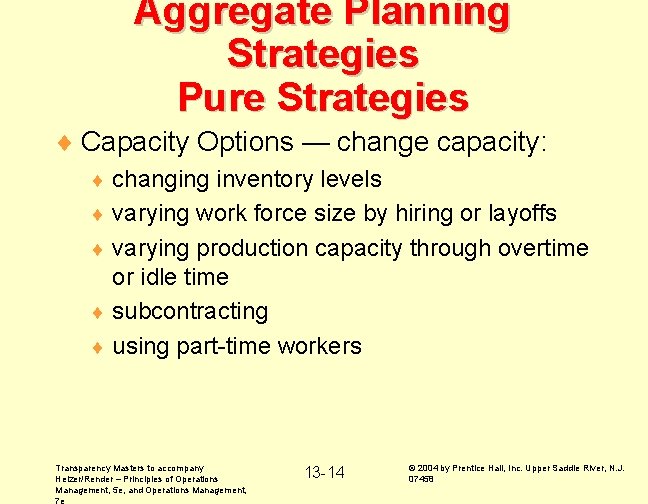



Operations Management Aggregate Planning Chapter 13 Transparency Masters
Basic aggregate planning strategies are Level Capacity Chase Demand Demand Time period (year) Maintaining a steady rate of output while meeting variations in demand by a combination of options Level Capacity Demand Time period (one year) Production Production Cumulative production Cumulative demand Cumulative output/demand Interesting Extra capacity may be obtained by subcontracting at an additional cost of $15 per unit over and above the company's producing them itself on regular time Provide a detailed cost breakdown for using a level vs a chase strategy to meet the increased demand2 4 Aggregate Planning Problem Given the demand forecast, determine the best dtill production level, inventory level, capacity level Specify the planning horizon duration of each period key required information 5
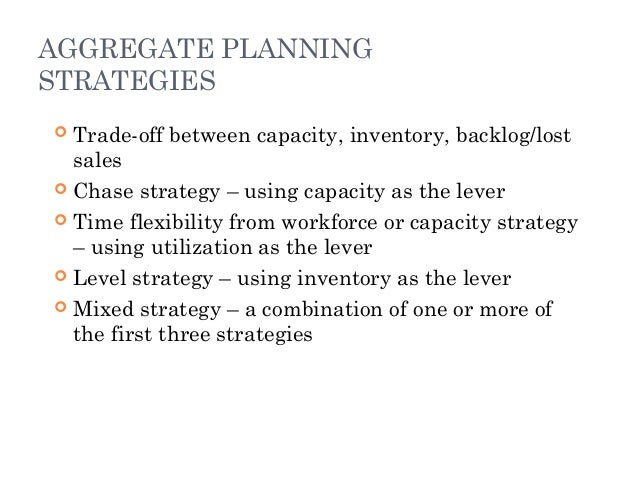



Aggregate Planning In The Supply Chain
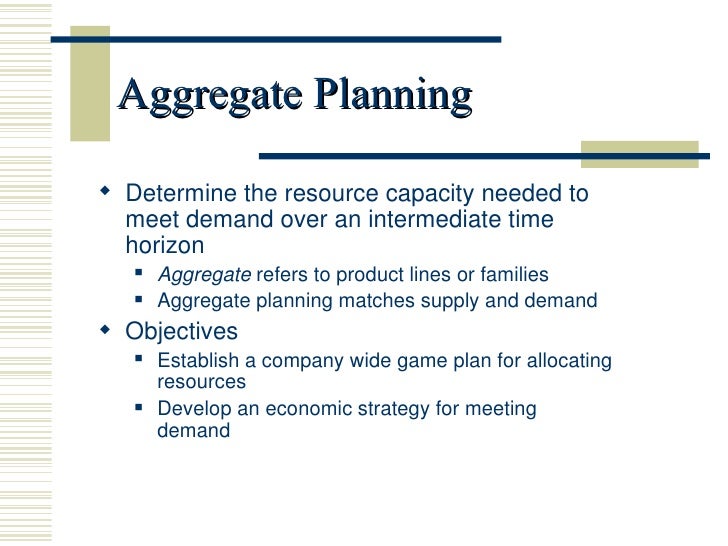



Aggregate Planning
Planning Aggregate Planning Master Scheduling Detailed Planning & Scheduling C A P A C I T Y P L A& N N I N G Business F O R E C A S T I N G D E M A N D Planning Source Wallace, Tom F Sales and Operations Planning, A HowTo Guide, TF Wallace & Co 1999 A level strategy seeks to produce an aggregate plan that maintains a steady production rate and/or a steady employment level They are Aggregate Demand and Aggregate capacity Aggregate Demand (AD) is the quantitative assessment of the requirement for all goods and services for a specific period of time at a given price level Aggregate capacity is the total amount of capacity required or available to carry out a function It also tells about the 3 best strategies for aggregate planningThey are level strategy,




D Aggregate Planning Uses The Adjustable Part Of Capacity To Meet Production Course Hero



Aggregate Planning Mps Capacity Planning Strategic Management Inventory
Aggregate planning examples San Aziz Example 1 A large distribution center must develop a staffing plan that minimizes the total cost using parttime workers Use chase and level strategy Capacity (regular time, overtime, subcontracted) Inventory Backlog/lost sales because of delay There are essentially three distinct aggregate planning strategies for achieving balance among these costs These strategies involve tradeoffs among capital investment, workforce size, work hours, inventory, and backlogs/lost salesThe Extremes Level Chase Strategy Strategy Production Production rate equals is constant demand Basic Aggregate Planning Strategies for Meeting Demand Level capacity strategy • Keeping work force constant and maintaining a steady rate of regulartime output while meeting variations in demand by a combination of options (such as using



Aggregate Production Planning Operations Management Homework And Assignment Help
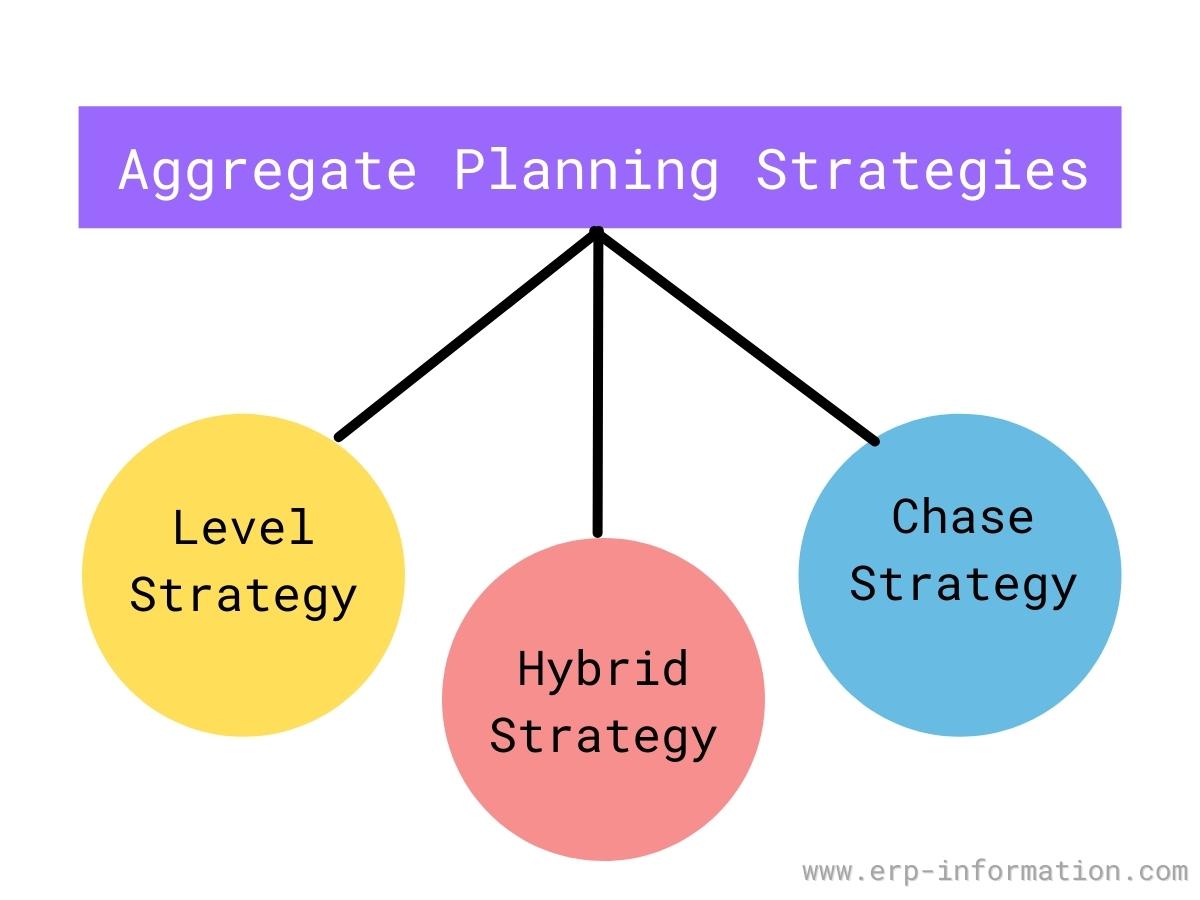



What Is Aggregate Planning 3 Strategies For Aggregate Production Planning
Aggregate planning is concerned with determining the quantity and the schedule of production for the immediate future Aggregate plans are intermediaterange plans that are valid for three to 18 months The main objective of aggregate plans is to lower costs and to use capacity most efficientlyAggregate planning is a marketing activity that does an aggregate plan for the production process, in advance of 6 to 18 months, to give an idea to management as to what quantity of materials and other resources are to be procured and when, so that the total cost of operations of the organization is kept to the minimum over that period The quantity of outsourcing, b Defining the concept of aggregate plan for operational capacity management, which strategy (Level or Chase) do you think would be best applicable for the company?



Aggregate Planning




Slides Show
(5 Marks) For NMIMS Assignments, Case study Answer sheets Project Report and Thesis contact email protected wwwmbacasestudyanswerscom ARAVIND – –The Aggregate Planning Problem •Given the demand forecast for each period in the planning horizon •Determine the production level, inventory level, and the capacity level for each period that maximizes the firm's (supply chain's) profit over the planning horizon •Specify the planning horizon (typically 318Key words Capacity strategy, Level capacity, Chase capacity and Capacity utilization 1 Introduction The economic significance of capacity utilization can be expressed in the level of demand If market demand grows, the rate of utilization of capacity will increase as it is expected that output will rise Also, if demand




Aggregate Planning 101 What You Need To Know Brendan Jones




Aggregate Planning
AGGREGATE PLANNING STRATEGIES There are three pure planning strategies available to the aggregate planner a level strategy, a chase strategy an workforce strategy Firms may choose to utilize one of the pure strategies in isolation, or they may opt for a strategy that combines the three LEVEL STRATEGY A level strategy seeks to produce an aggregate planIn doing "aggregate planning" for a firm producing paint, the aggregate planners would most likely deal with a forecast of expected demand, current levels of inventory, policies regarding employment levels In order to use the "level capacity strategyHowever, it is feasible to hire or lay off workers, increase or reduce the work week,



Web Uettaxila Edu Pk Cms Meie2bs Notes 5c01b Aggregate planning strategies Pdf



Http Www1 Pu Edu Tw Ylai Erp Dom 1042 Ppts S16 1042 Erp Dom Ap S16 Pdf
Level Strategy Costs Regular production costs Inventory carrying costs Hiring Costs Total Incurred Costs _____ The aggregate planning that we are going to carry out will among other things attempt to match the level of bike supply to demand It is going to determine the required quantities and the timing of inputs as well as outputsAggregate planning is capacity planning that typically covers a time horizon of one to three months
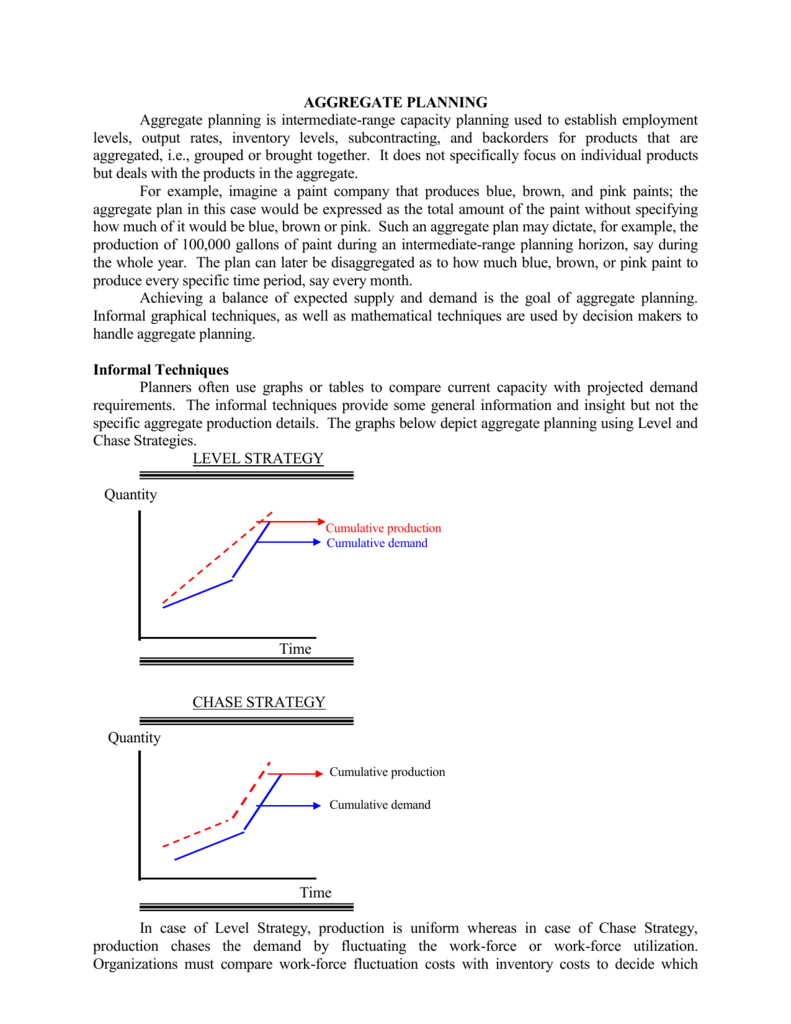



Aggregate Planning




Aggregate Planning



Sustainability In Supply Chain Management Aggregate Planning From Sustainability Perspective
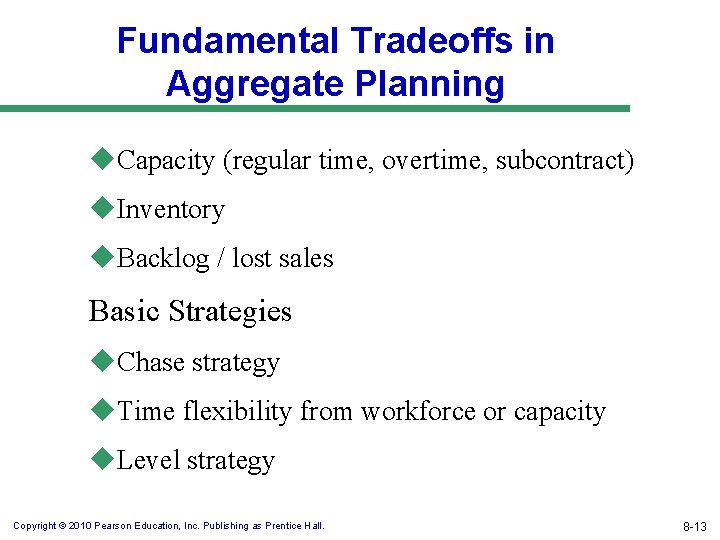



Chapter 8 Aggregate Planning In The Supply Chain




Capacity Planning Organization System Examples Definition System Long Term Capacity Planning
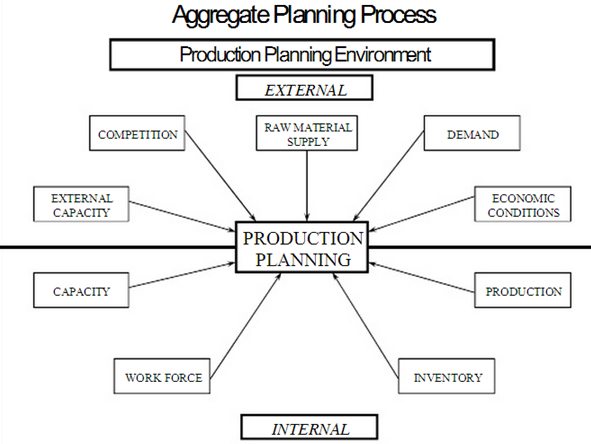



Aggregate Production Planning Aggregate Planning Process Aggregate Production Planning Strategies



1
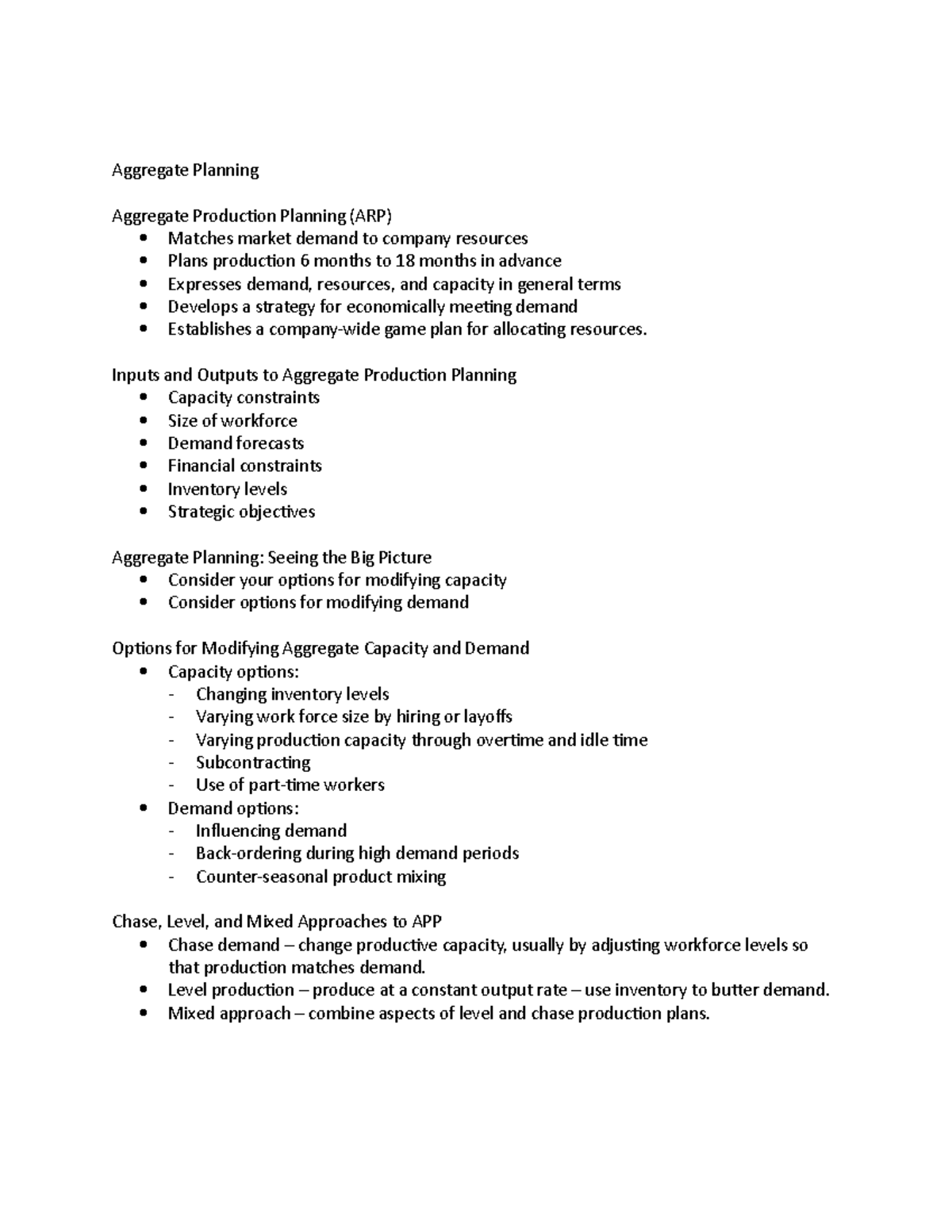



Aggregate Planning Lecture Notes 10 14 Studocu
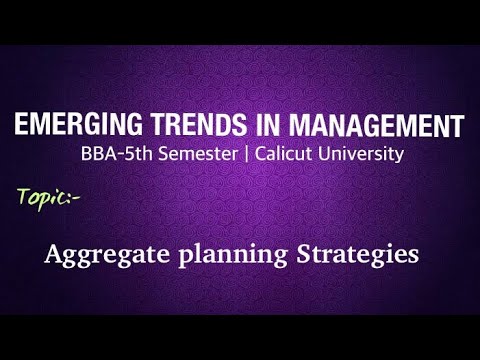



Aggregate Planning Strategies Chase Strategy Capacity Strategy Level Strategy a 5th Sem Cu Youtube
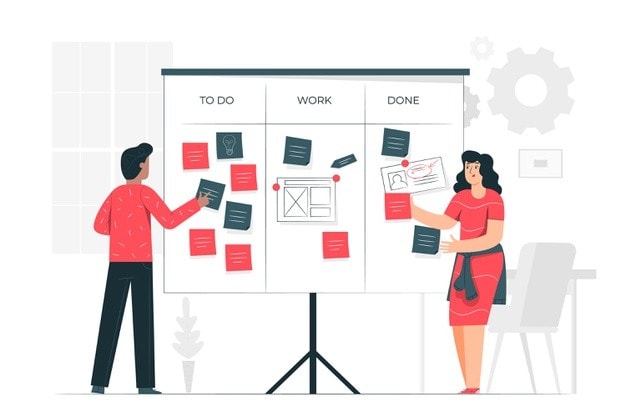



Aggregate Planning Definition Importance Strategies Management And Advantages
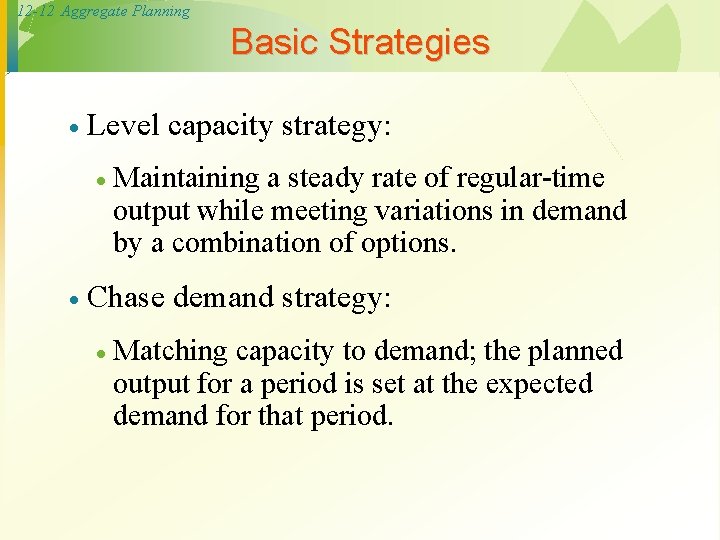



12 1 Aggregate Planning Operations Management William J
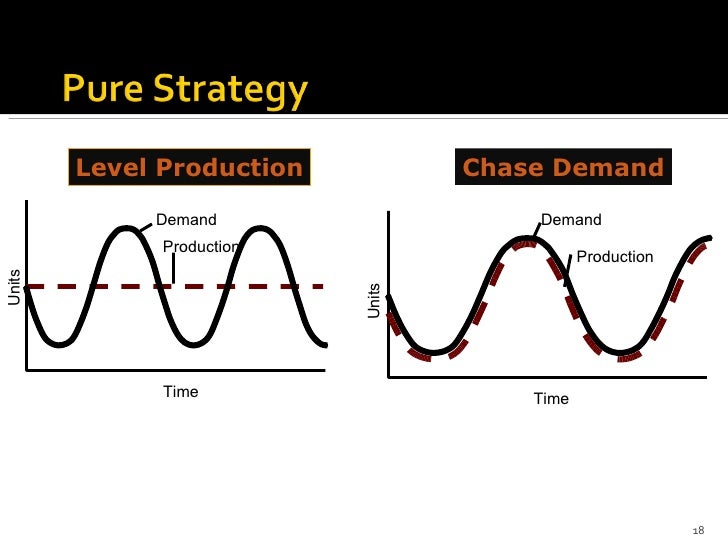



Productionplanning Aggregate Capacity




Operations Management Aggregate Planning Chapter Ppt Video Online Download
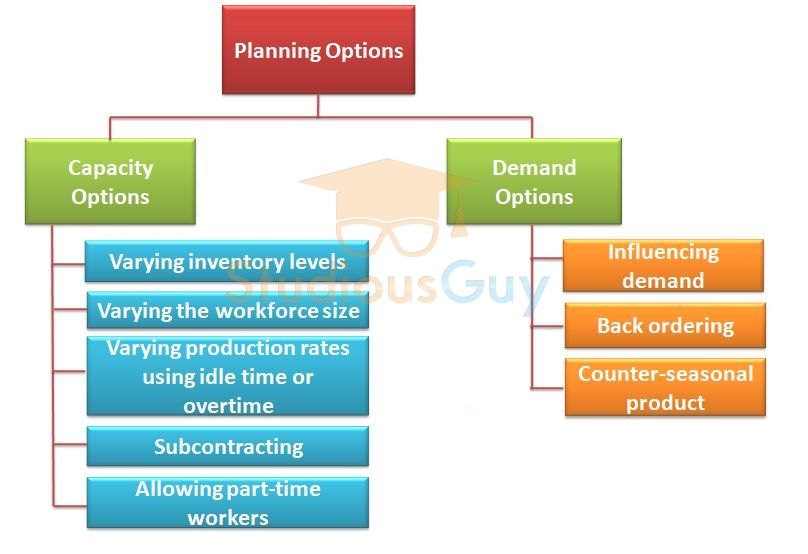



Aggregate Planning Studiousguy
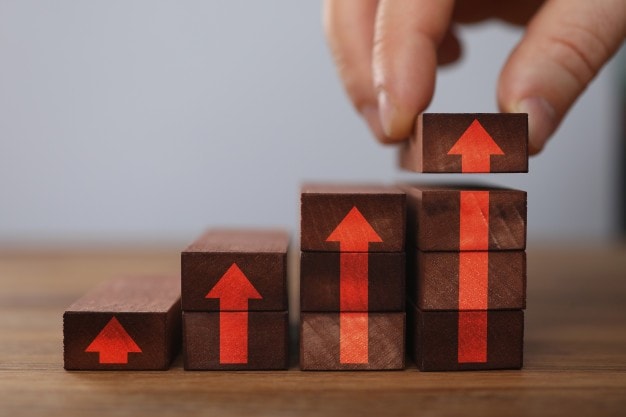



Aggregate Planning Definition Importance Strategies Management And Advantages
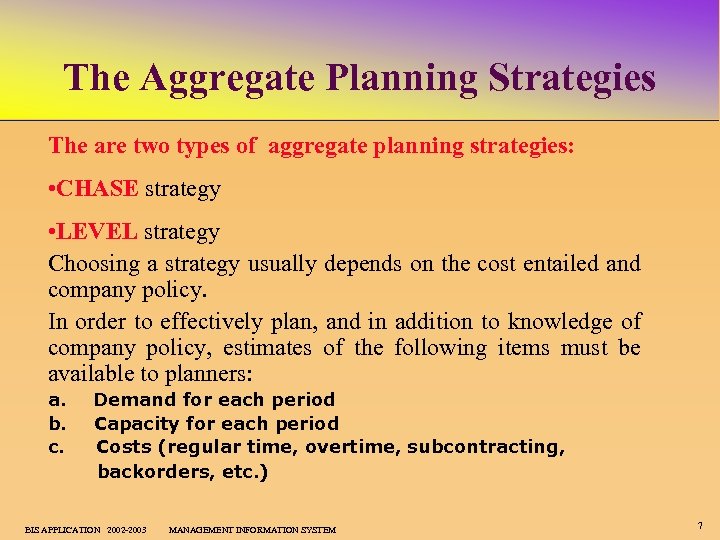



Aggregate Planning And Learning Curves Chapter Outline 1
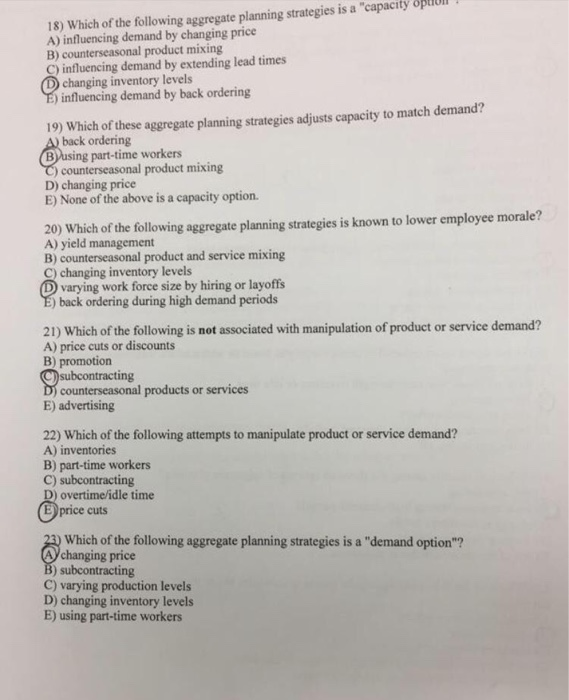



M Which Of The Following Is The Term Used For Medium Chegg Com




Production Planning Control Chapter 2 Aggregate Planning Master Production Scheduling Chapter2 1 Pdf Free Download




1 Dsci 4743 Inputs And Outputs To Aggregate Production Planning Aggregate Production Planning Company Policies Financial Constraints Strategic Objectives Ppt Powerpoint




Operations Management Chapter Multiple Choice Problems Flashcards Quizlet
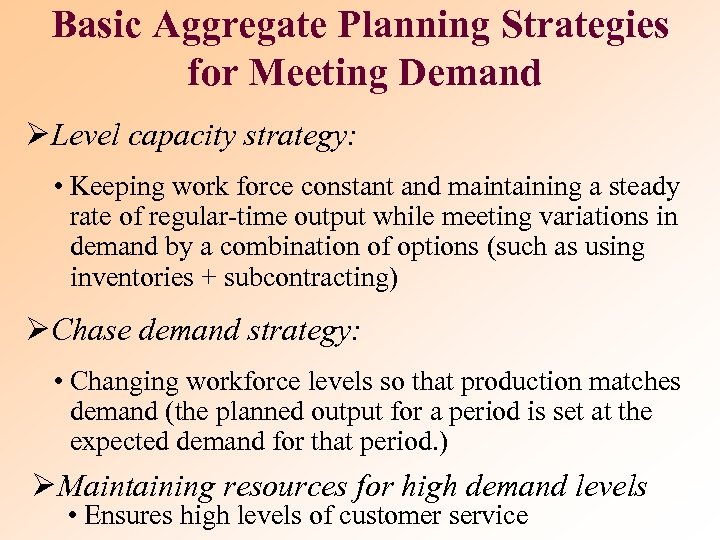



Aggregate Planning Planning Horizon Aggregate Planning Intermediate Range
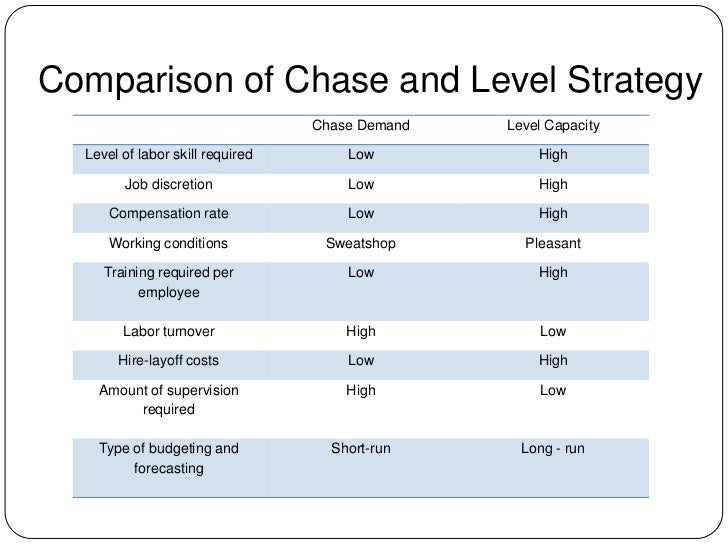



Aggregate Planning Report




Sales And Operations Planning Aggregate Planning Production Planning Operations Planning How To Meet Effectively And Efficiently Forecasted Requirements Ppt Video Online Download
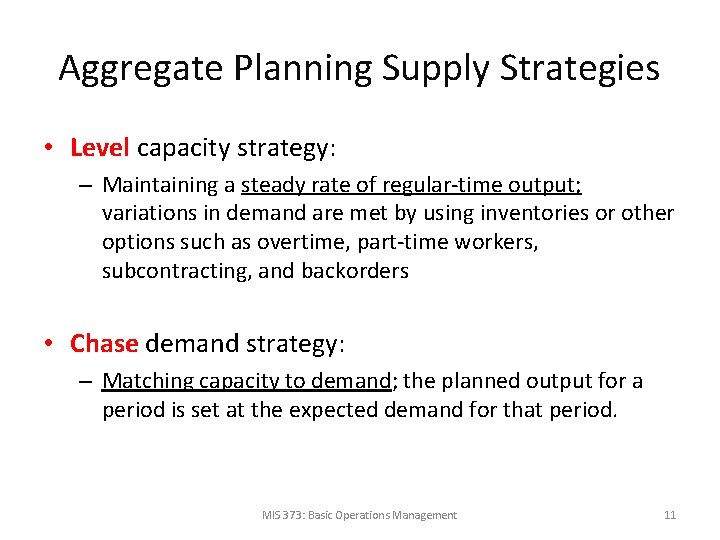



Aggregate Planning Chapter 11 Aggregate Planning Aggregate Planning




Aggregate Planning Strategy Organization Levels System Examples Model Type Company System



Master Production Schedule
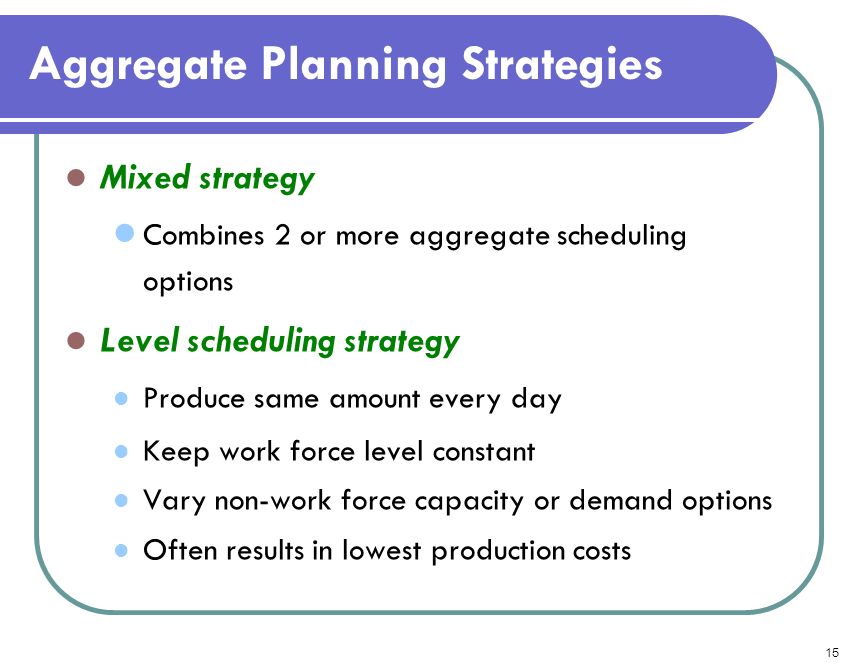



Operations Management Aggregate Planning Ppt Download



1




Aggregate Planning Strategy Organization Levels System Examples Model Type Company System




Chapter 12 Aggregate Planning Site Describe Ways To Dis Aggregate Aggregate Plans Using Master Production Aggregate Production Plan Option 1 Constant Workforce Without Pdf Document
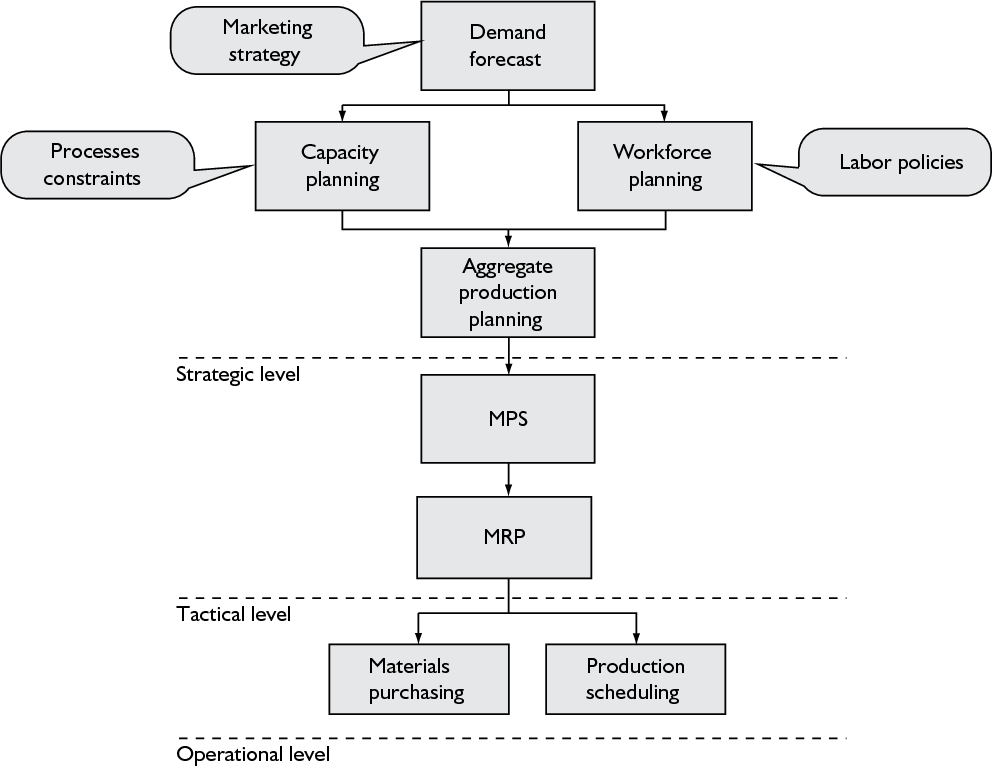



Aggregate Planning For A Large Food Manufacturer With High Seasonal Demand Semantic Scholar




Aggregate Planning Chapter 11 Mis 373 Basic Operations Management Ppt Download




Pdf Aggregate Production Planning For A Pump Manufacturing Company Level Strategy
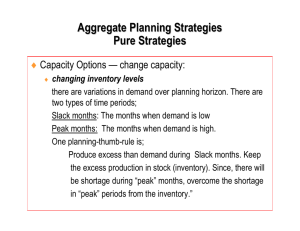



Chapter 13 Aggregate Planning



M Dc Operations Strategy



Http Www1 Pu Edu Tw Ylai Erp Dom 1042 Ppts S16 1042 Erp Dom Ap S16 Pdf
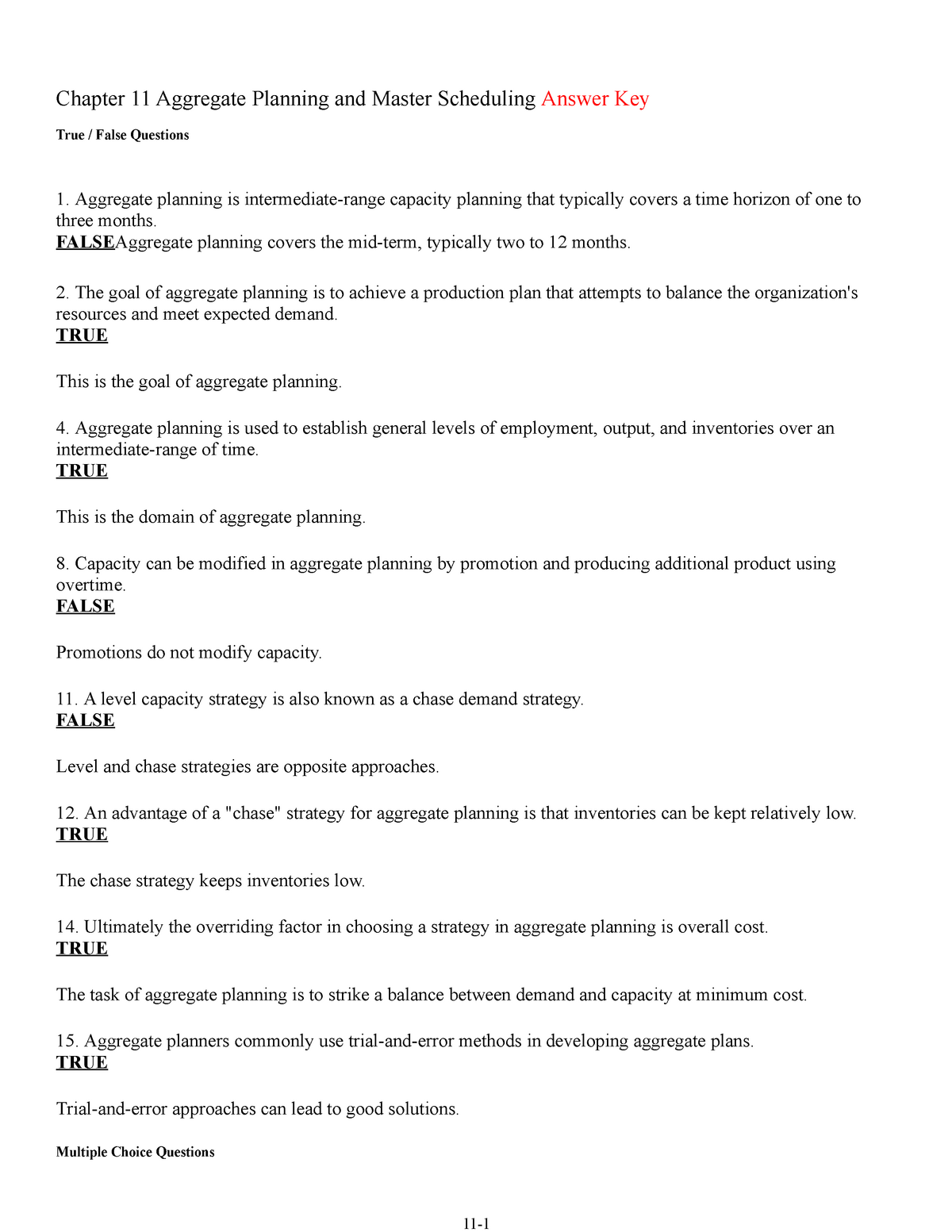



Chap011 Aggregate Chapter 11 Aggregate Planning And Master Scheduling With Answers Studocu
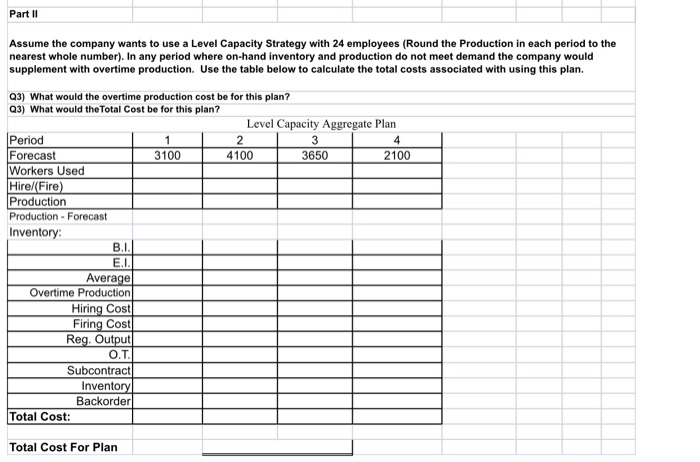



Solved Part Ii Assume The Company Wants To Use A Level Ca Chegg Com



Aggregate Planning Inventory Labour Economics
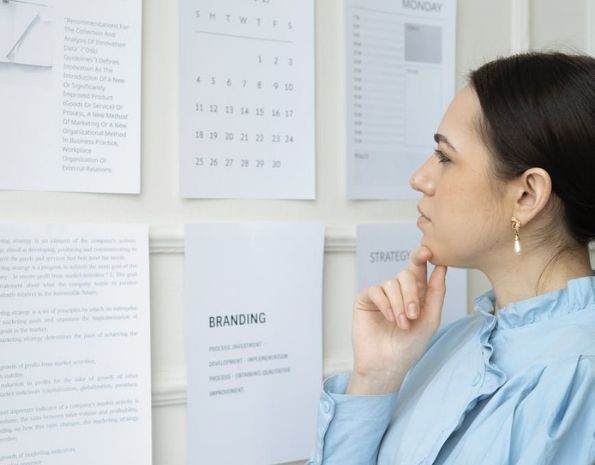



Aggregate Planning Strategies Methods And Examples Harappa Education
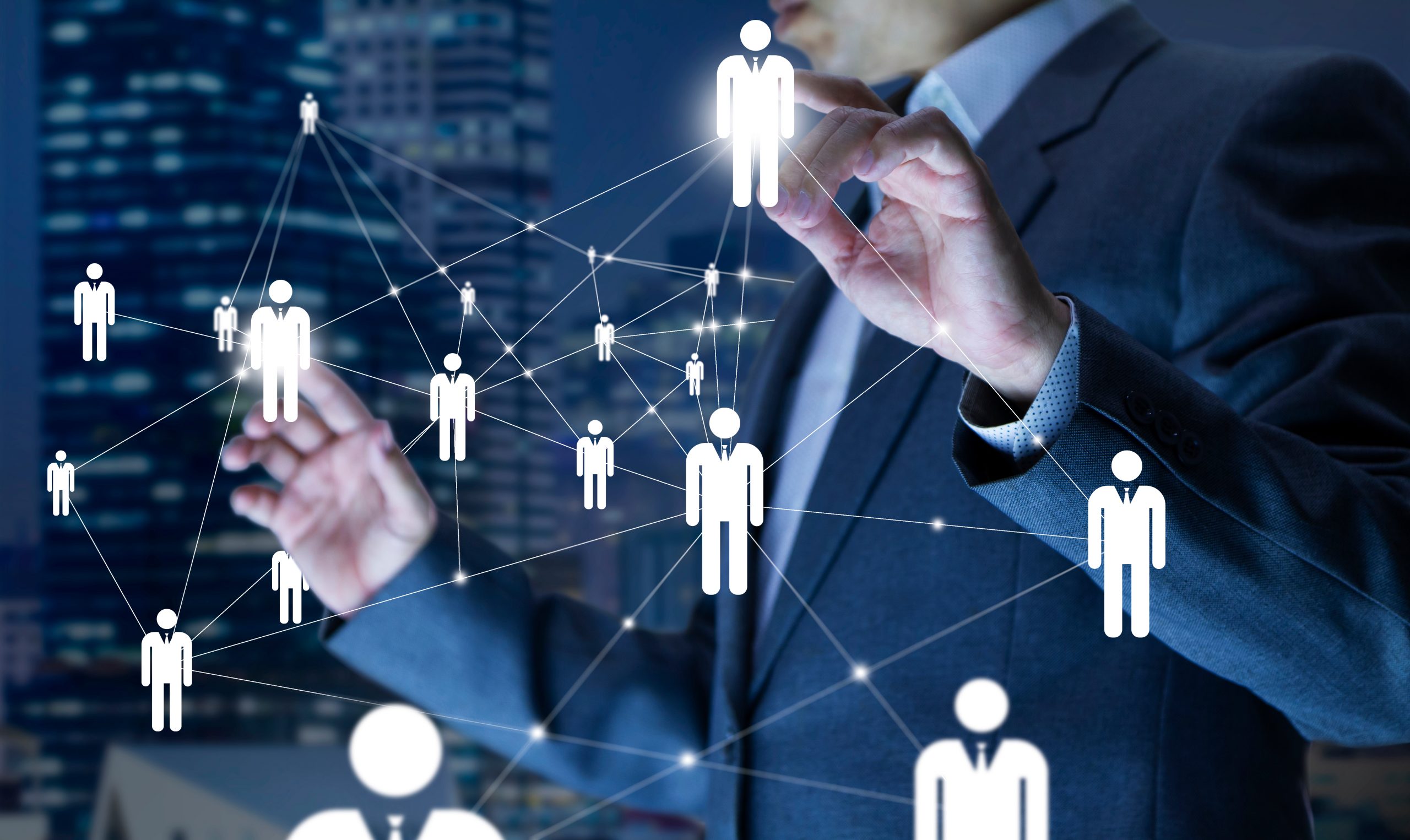



Top 5 Production Capacity Planning Challenges You Should Know Plex Demandcaster




Master Production Schedule An Overview Sciencedirect Topics




Everything About Capacity Planning Strategies Its Benefits



1



Http Csbapp Uncw Edu Janickit Ops370 Modules Module10 Pdf
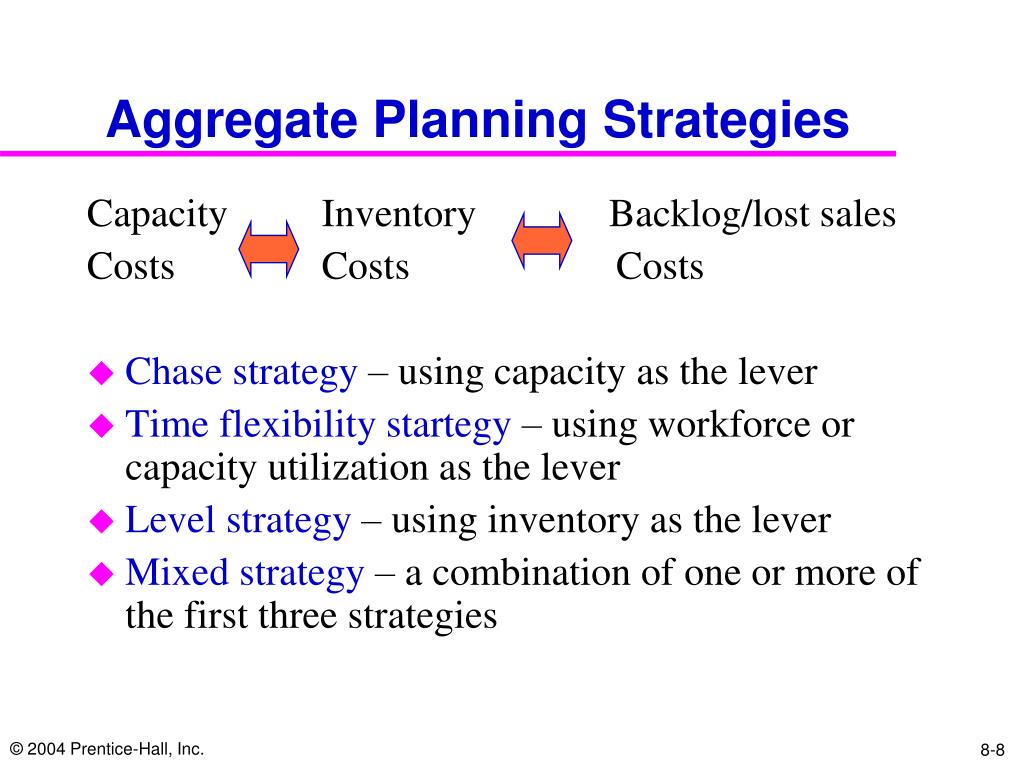



Ppt Chapter 8 Aggregate Planning In The Supply Chain Powerpoint Presentation Id




Aggregate Capacity Planning Pdf Free Download



1
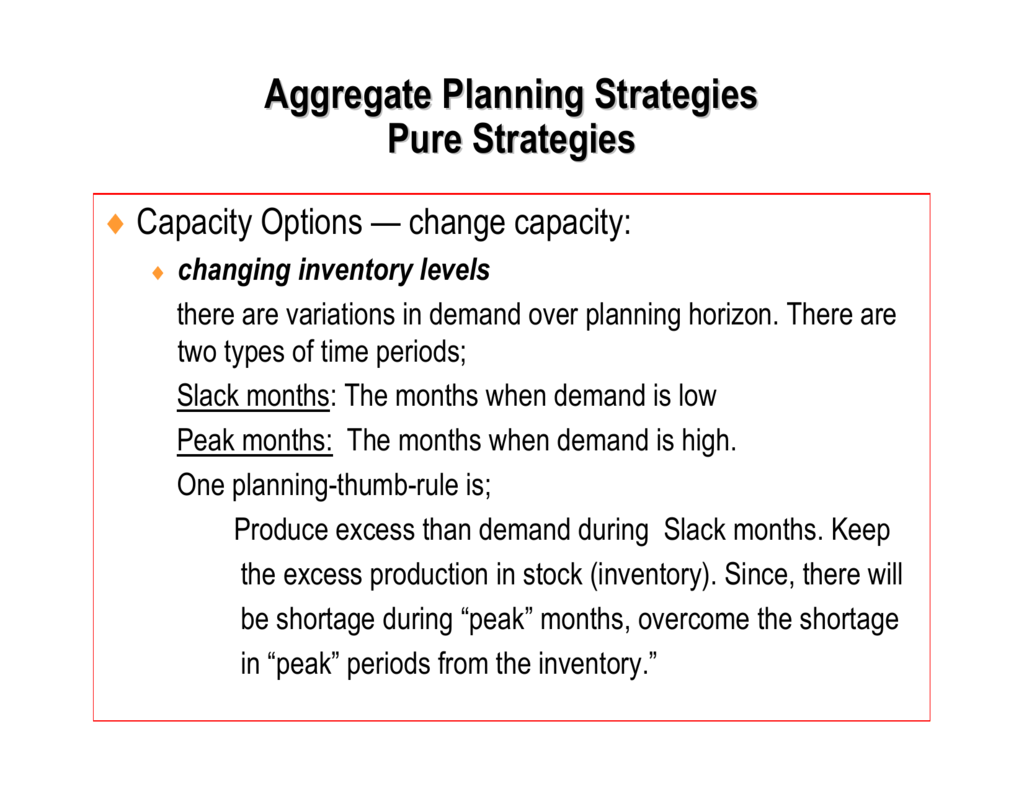



Aggregate Planning Strategies Pure Strategies
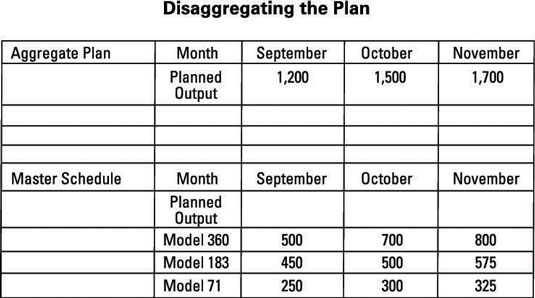



The Components Of An Operations Management Aggregate Plan Dummies



Myclass Dau Edu cswebdav Xid 4 2
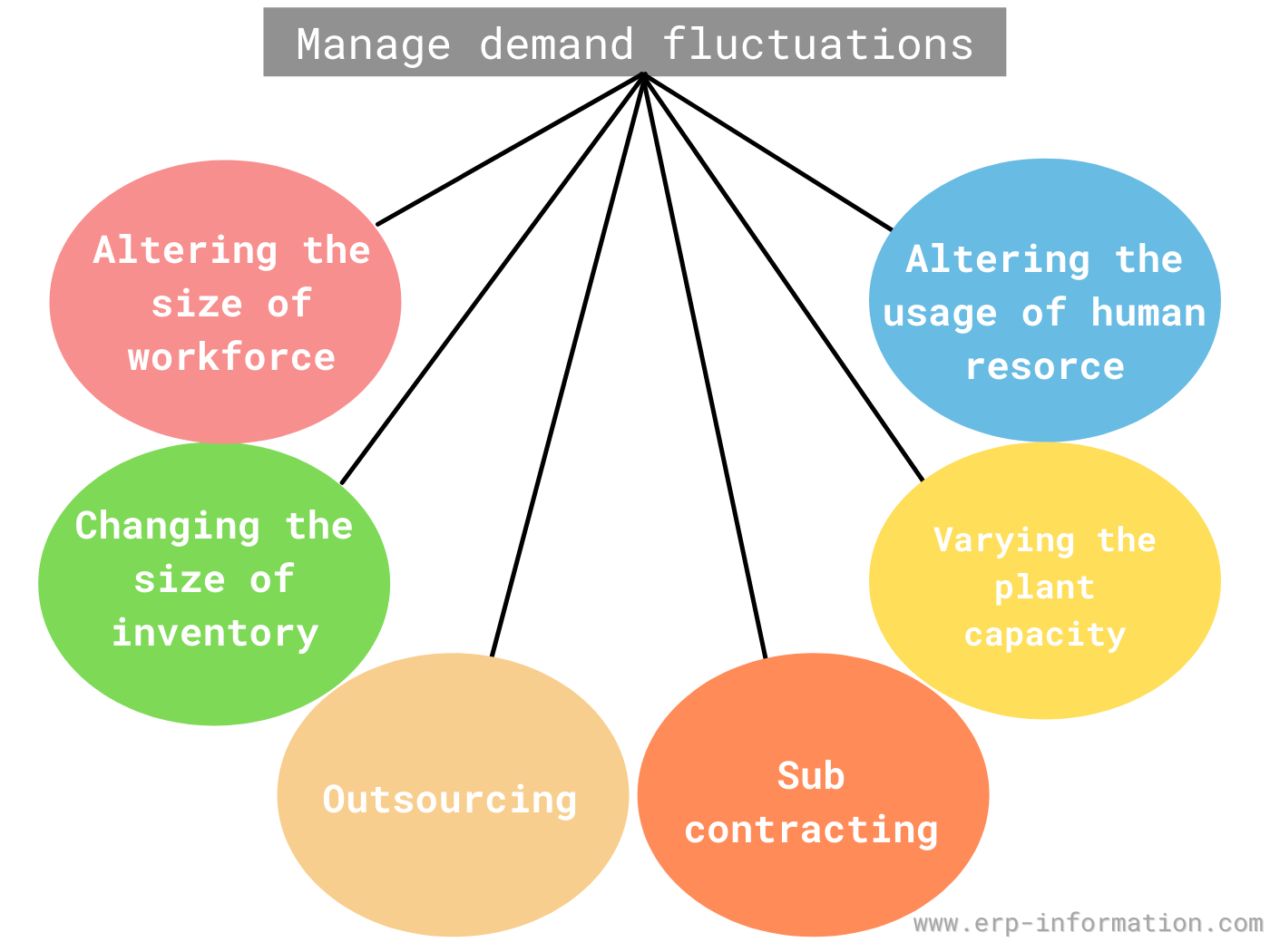



What Is Aggregate Planning 3 Strategies For Aggregate Production Planning




Aggregate Planning 101 What You Need To Know Brendan Jones
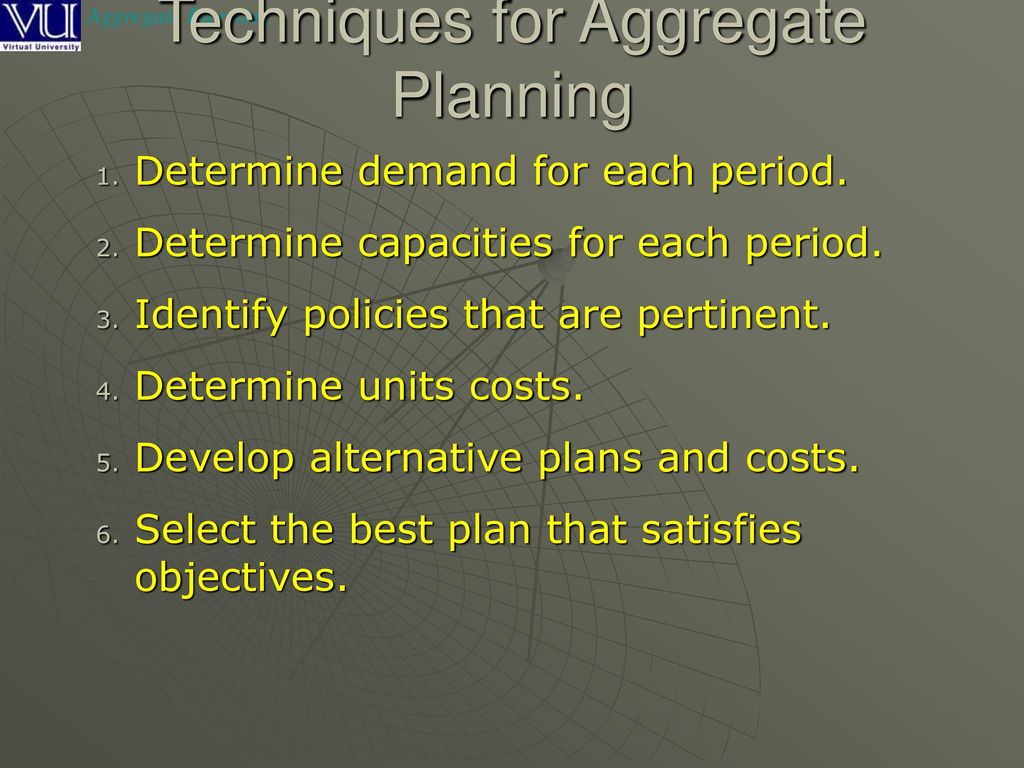



Basic Strategies Level Capacity Strategy Chase Demand Strategy Ppt Download
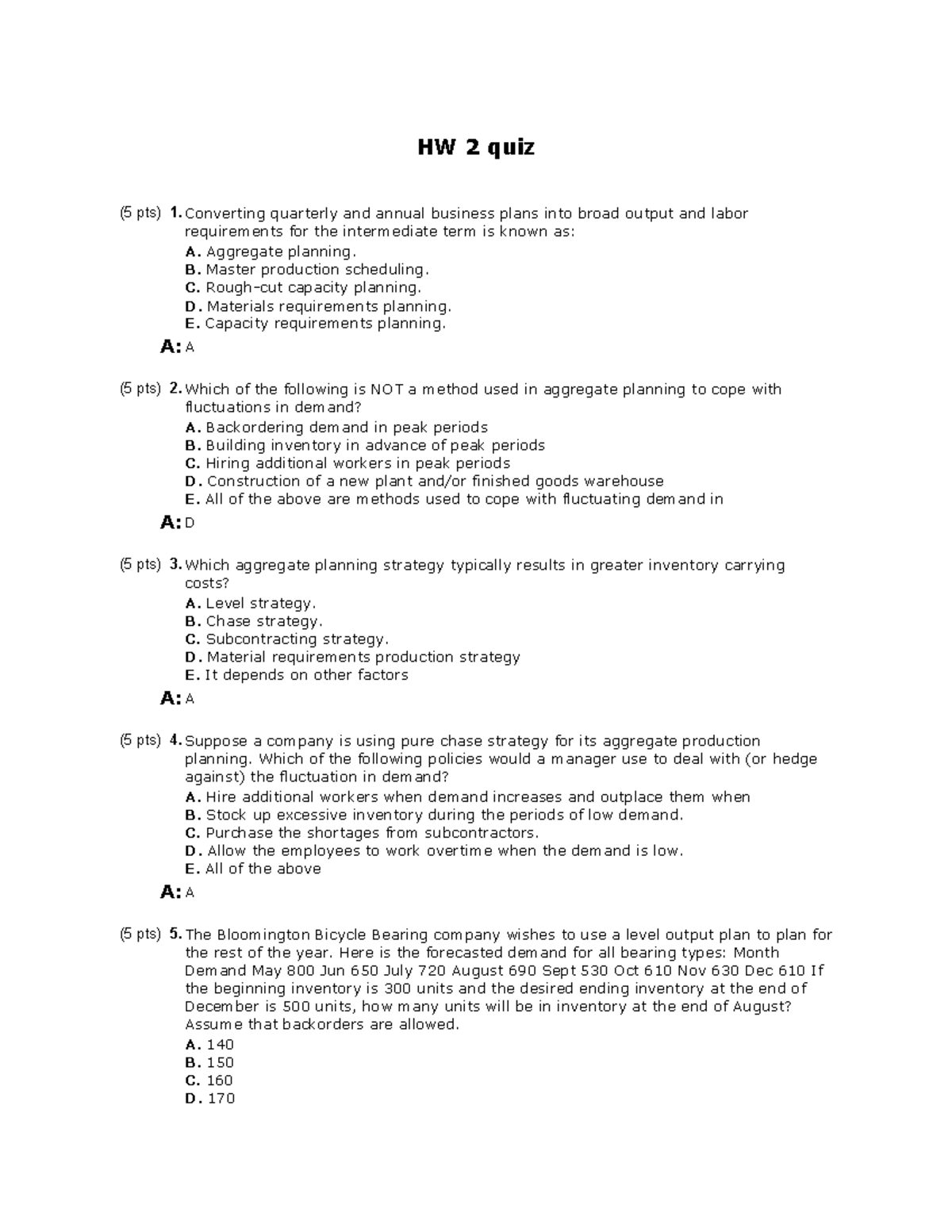



Hw2 Quiz With Answers Hw Quiz Pts Converting Quarterly And Annual Business Plans Into Broad Output And Labor Requirements For The Intermediate Term Is Known As Studocu



Sihombing15 Files Wordpress Com 08 08 Ch 7 Aggregate Capacity Planning Pdf



Methods For Aggregate Planning Inventory Labour Economics



Aggregate Planning Strategies Of Scm Inventory Demand
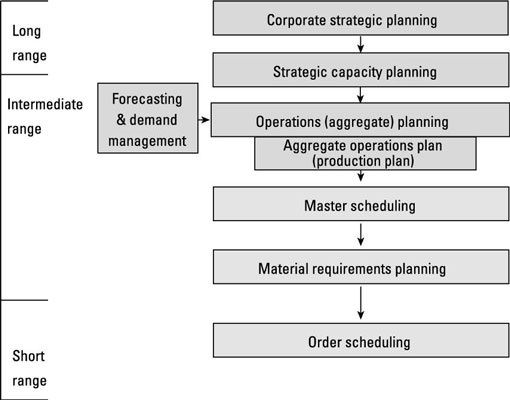



The Components Of An Operations Management Aggregate Plan Dummies
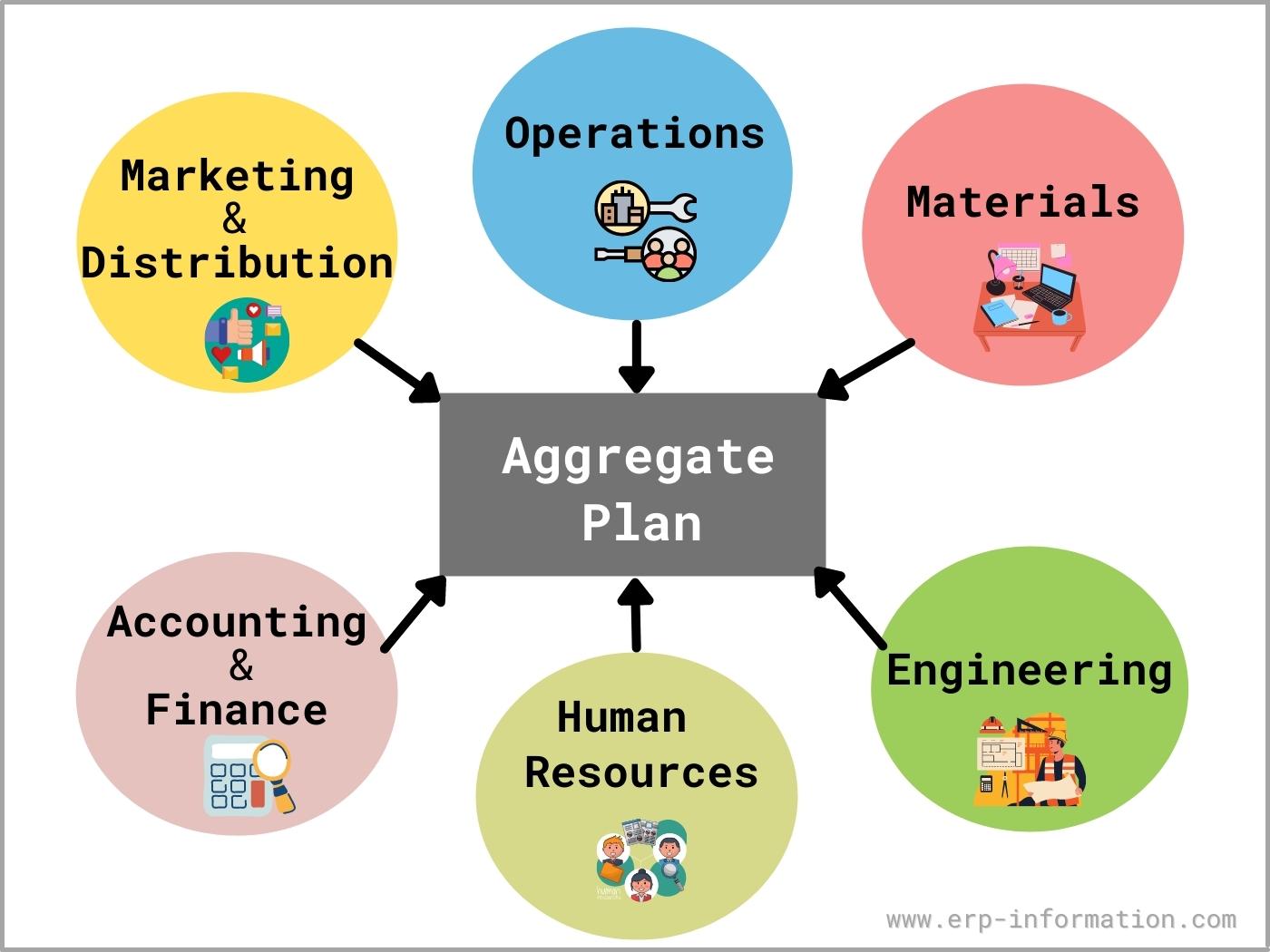



What Is Aggregate Planning 3 Strategies For Aggregate Production Planning
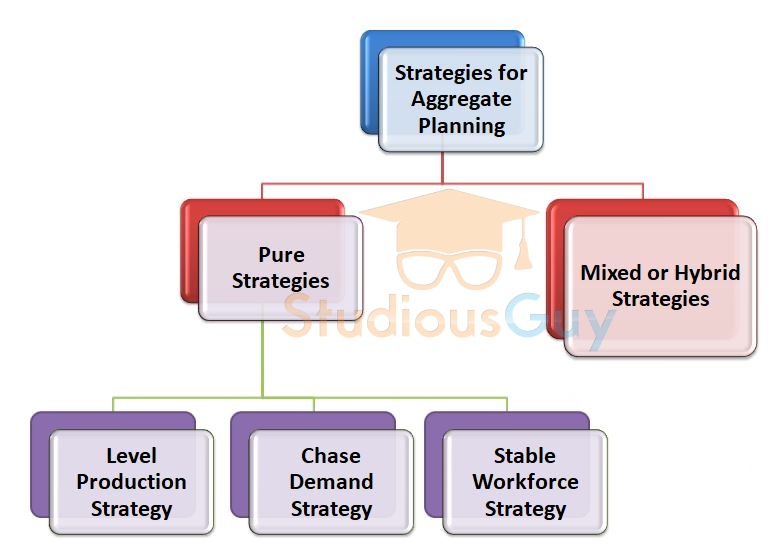



Aggregate Planning Studiousguy



Http Site Iugaza Edu Ps Aschokry Files 11 09 Om Chap 13 Aggr Plan2 Pdf




Which Of These Aggerate Planning Strategies Is A Capacity Option Nadex Cfpb Complaint
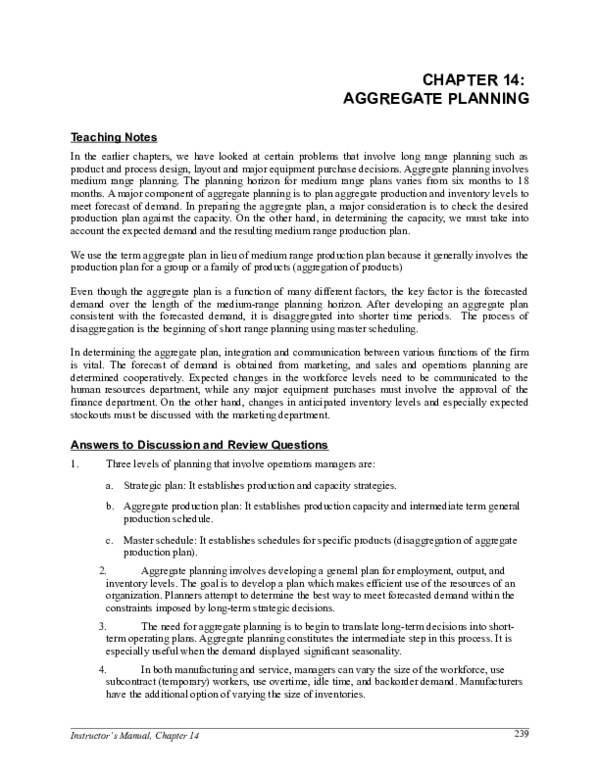



Doc Chapter Stuti Agrawal Academia Edu
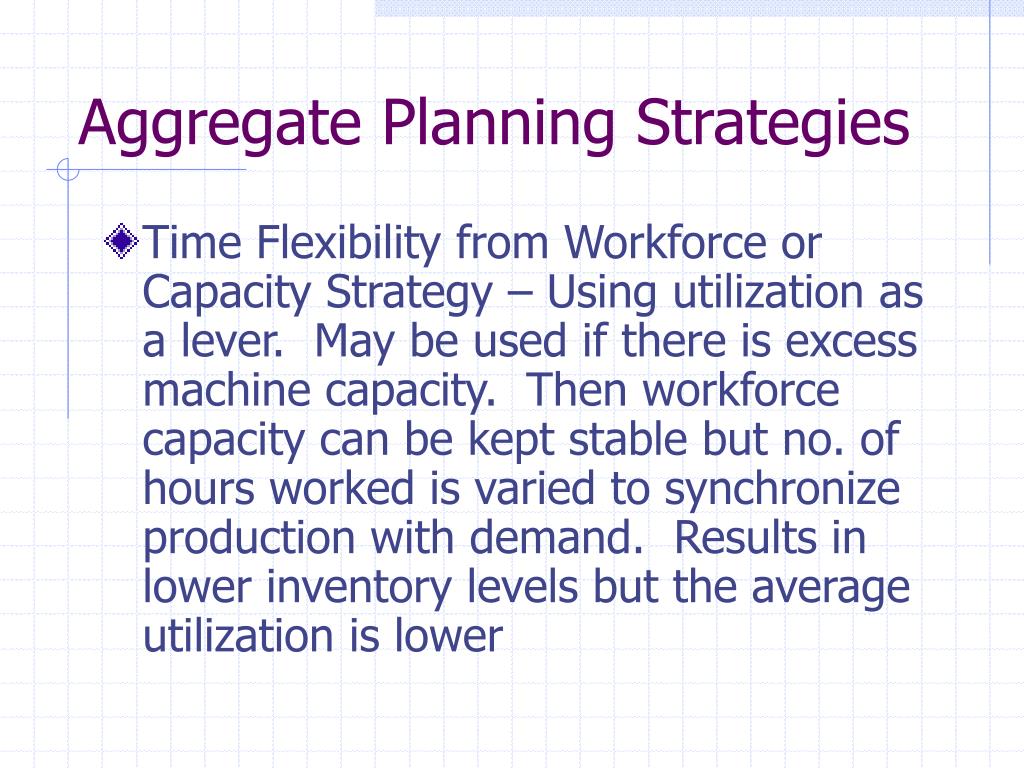



Ppt Aggregate Planning Powerpoint Presentation Free Download Id




Disadvantages Of Aggregate Planning Advantages And Disadvantages Of Aggregate Production Planning
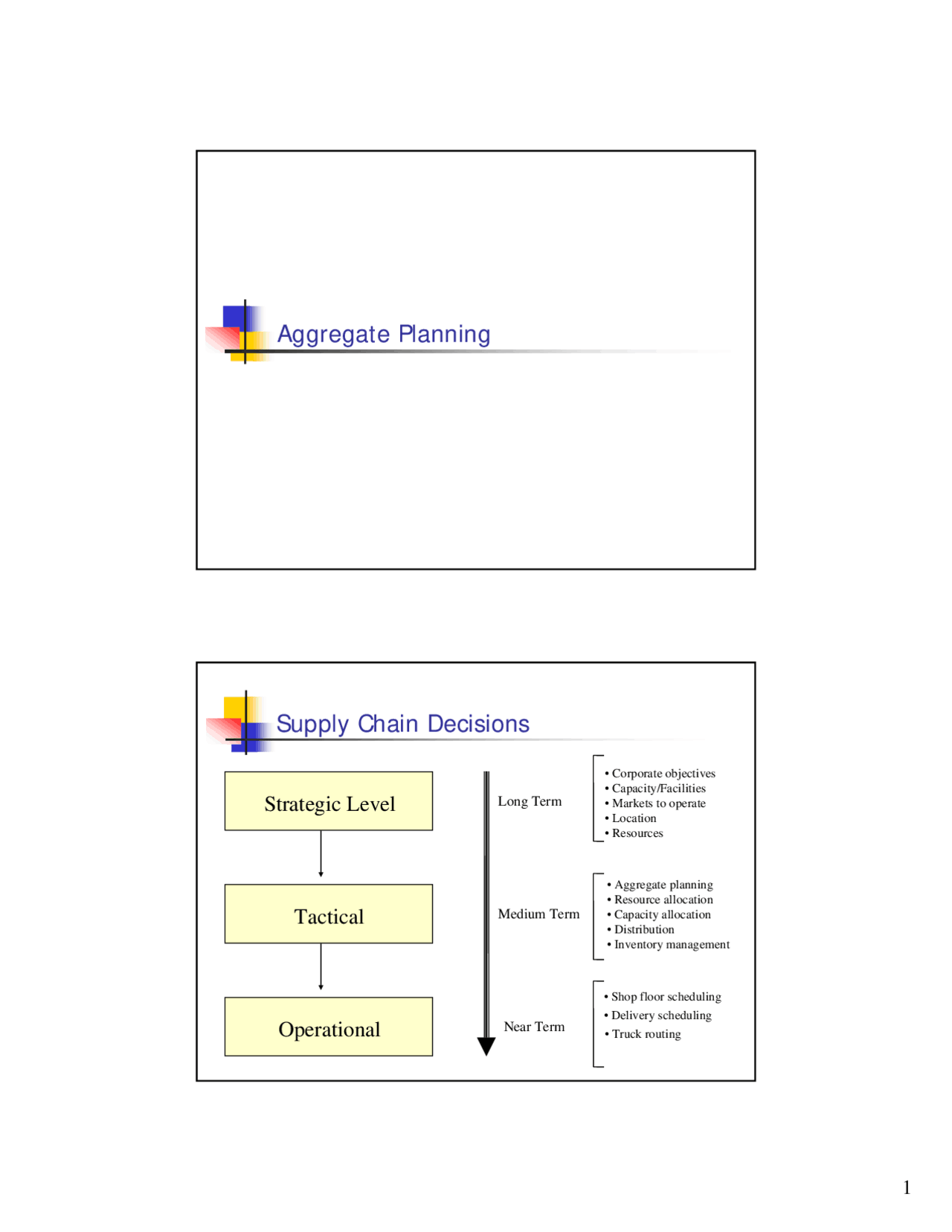



Aggregate Planning Lecture Slides Isye 3104 Docsity




Master Production Schedule An Overview Sciencedirect Topics




Safety Stock In Inventory Systems Depends Only On The Average Demand During The Course Hero
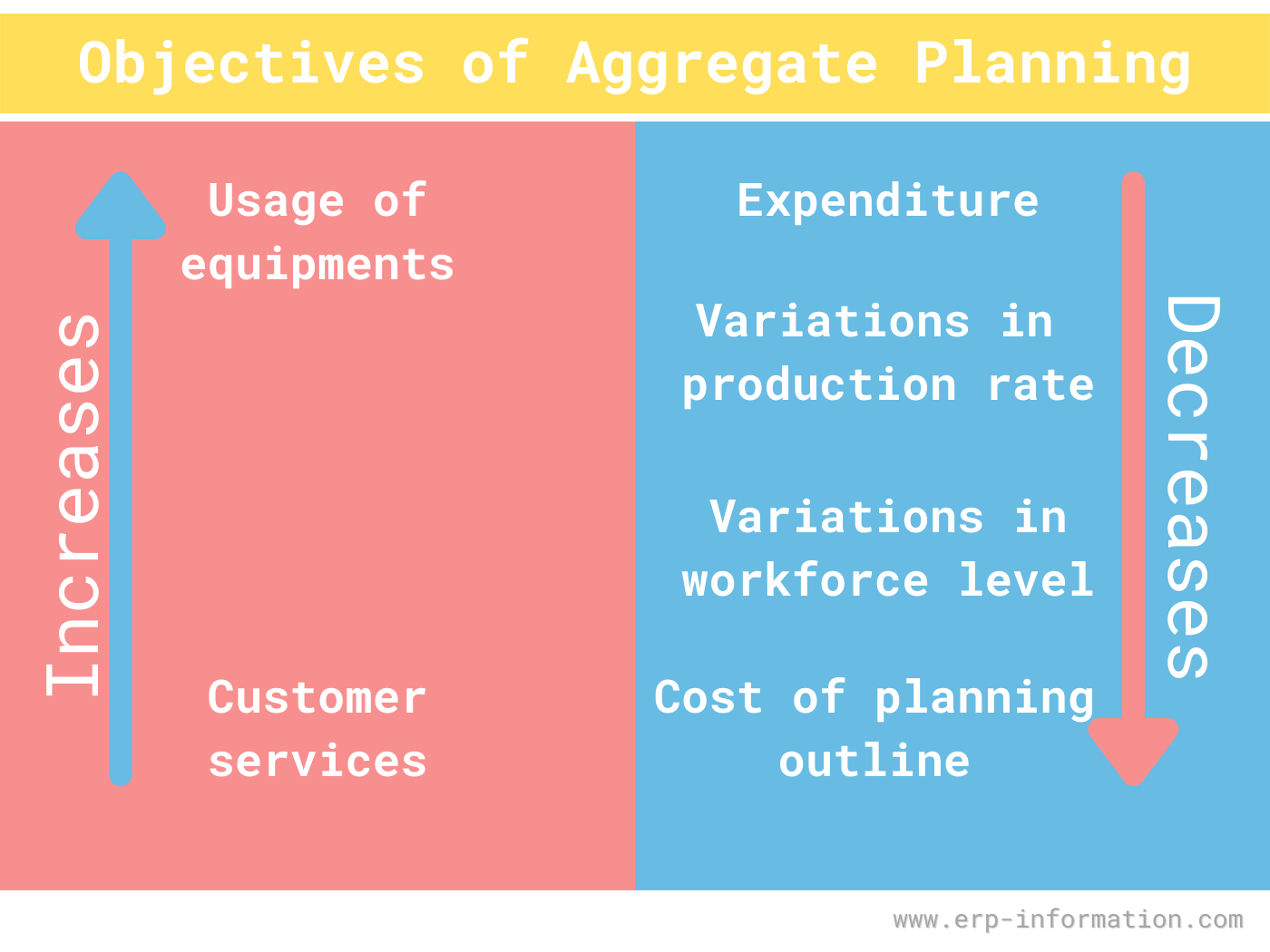



What Is Aggregate Planning 3 Strategies For Aggregate Production Planning




Aggregate Planning Strategy Organization Levels System Examples Model Type Company System
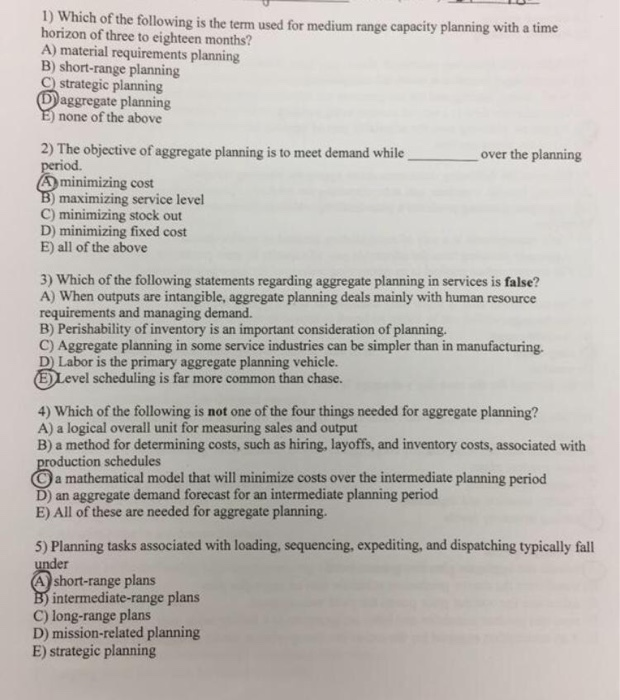



M Which Of The Following Is The Term Used For Medium Chegg Com
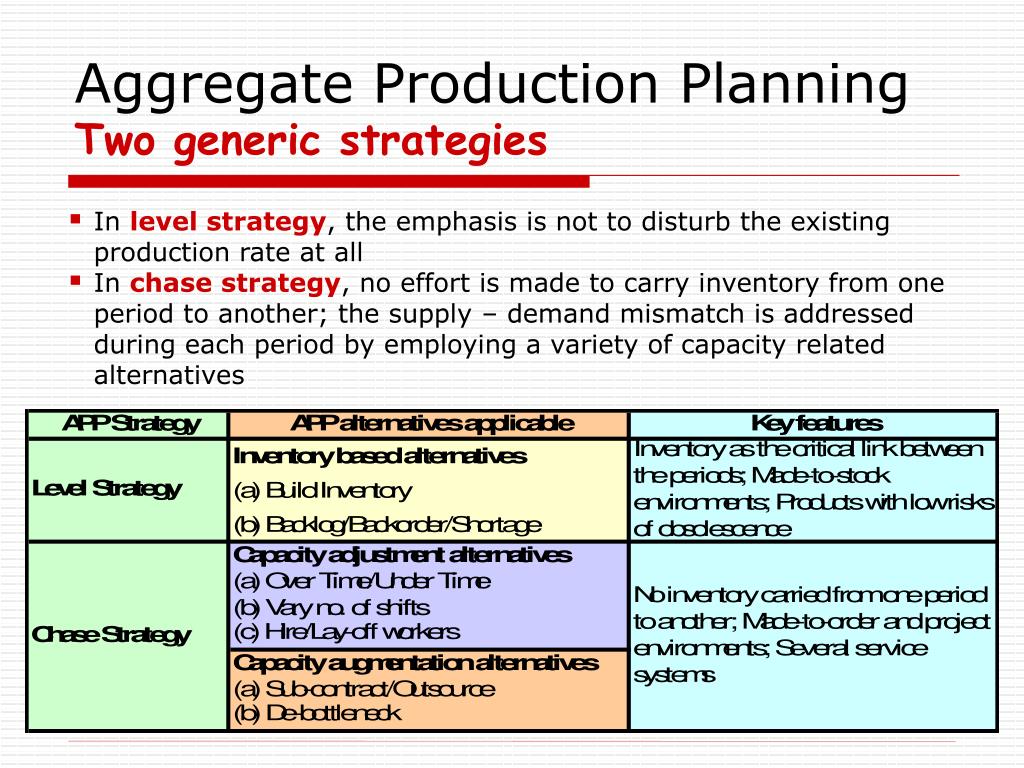



Ppt Aggregate Production Planning Powerpoint Presentation Free Download Id
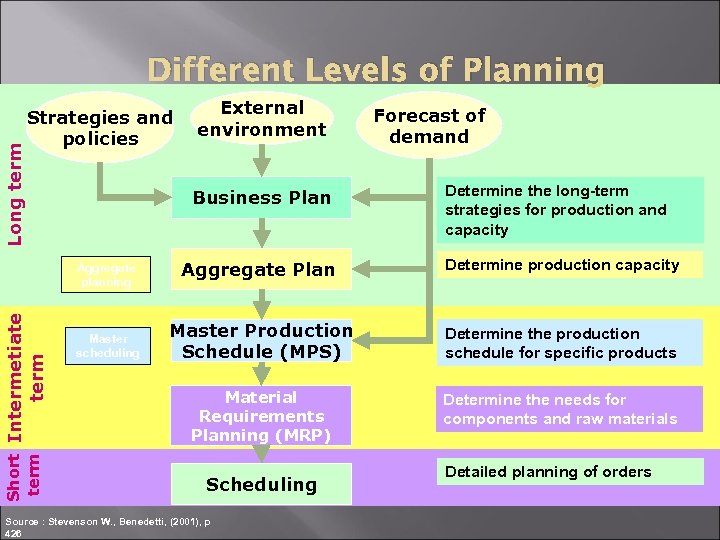



Production Planning And Control The Objectives Of
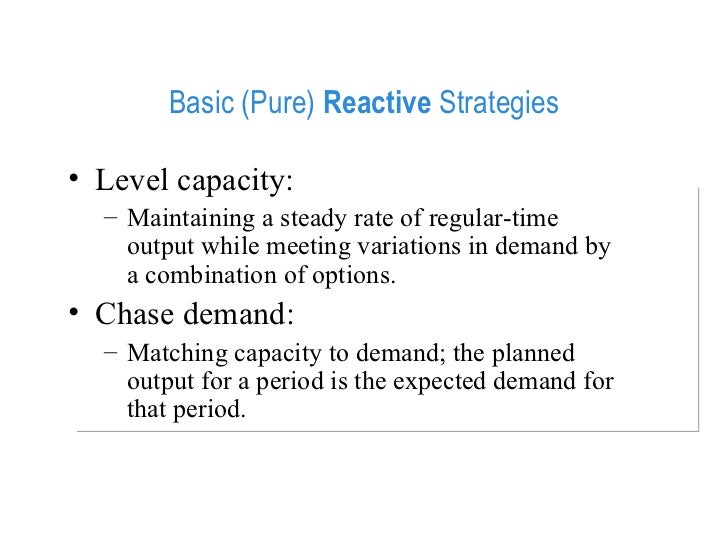



Aggregate Planning
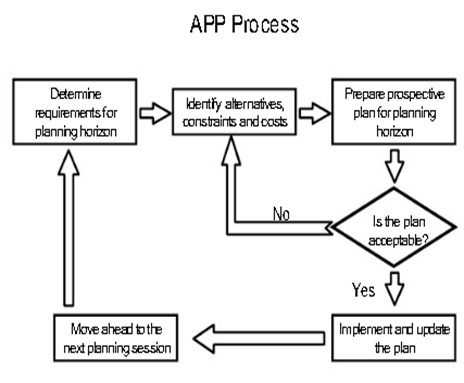



Aggregate Production Planning Aggregate Planning Process Aggregate Production Planning Strategies
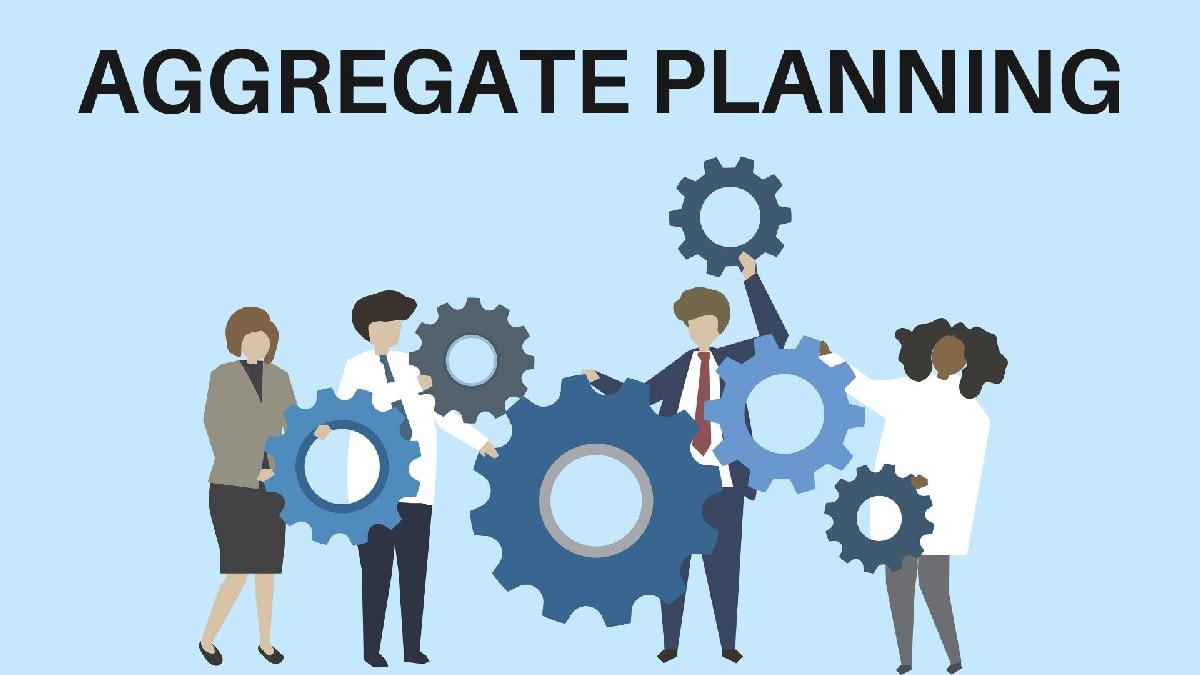



Aggregate Planning Definition Importance Strategies Management And Advantages
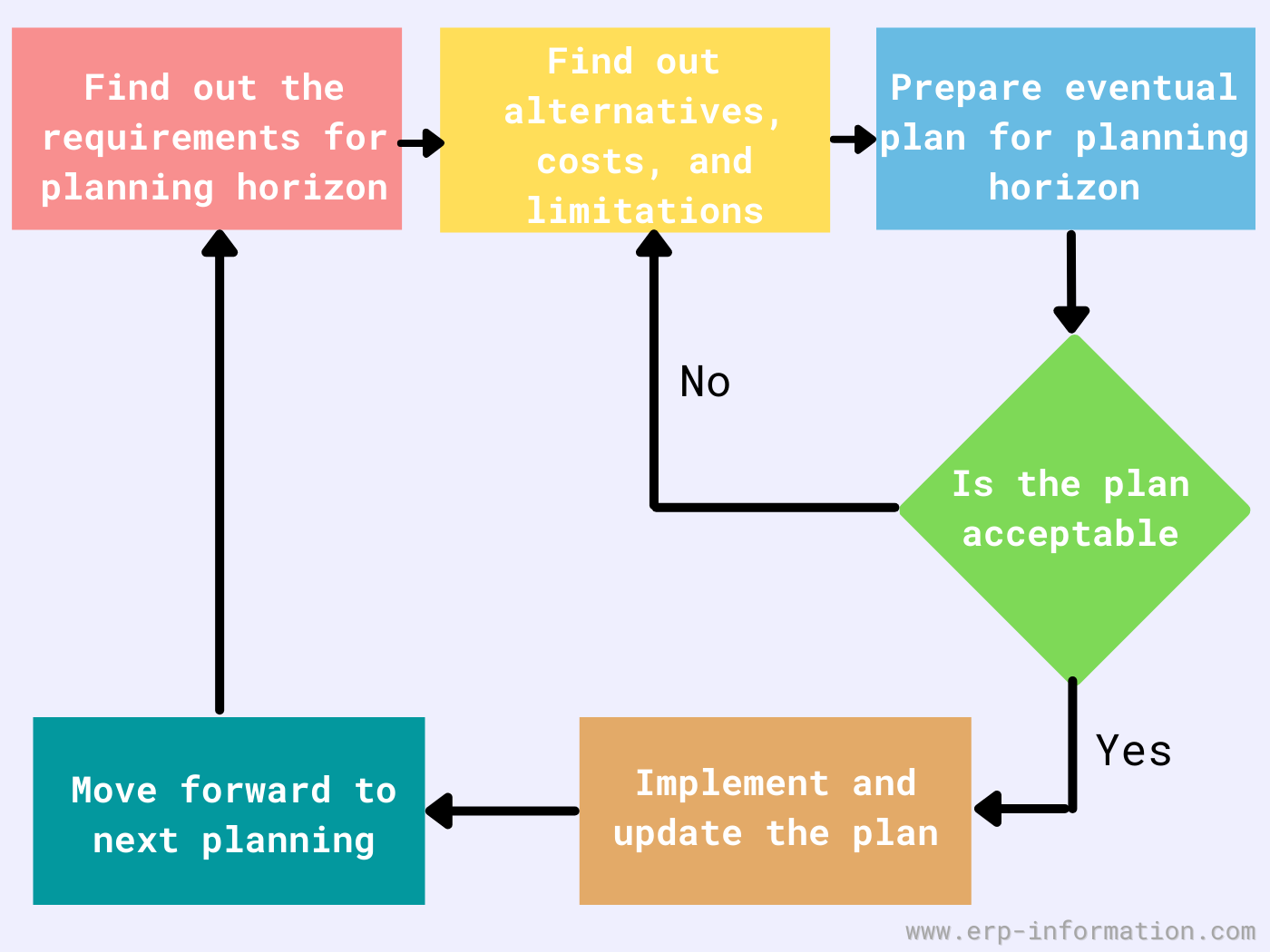



What Is Aggregate Planning 3 Strategies For Aggregate Production Planning




Sap Integrated Business Planning Ibp Sales And Operations Planning 18 Sap Blogs
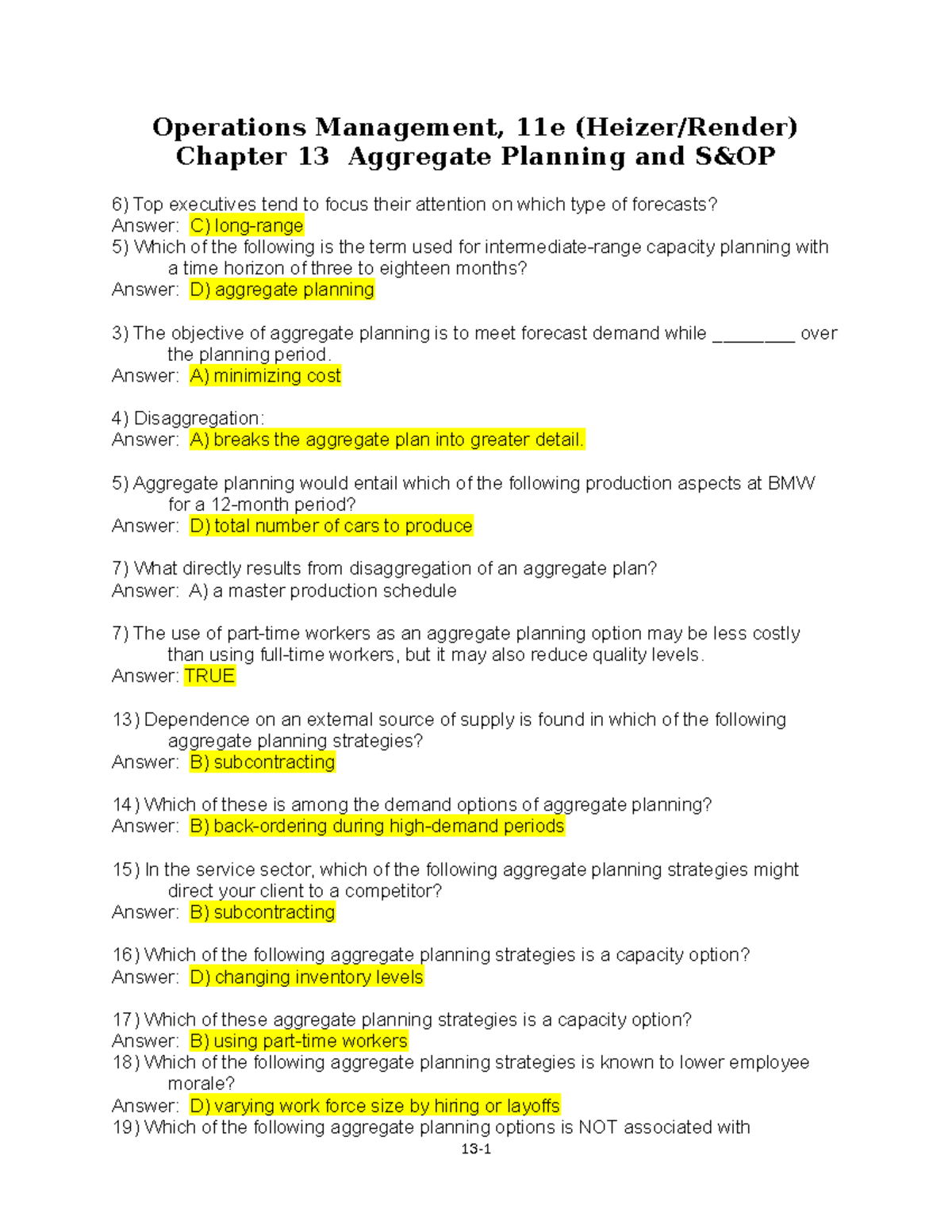



Mgt 3110 Chapter 13 Studocu
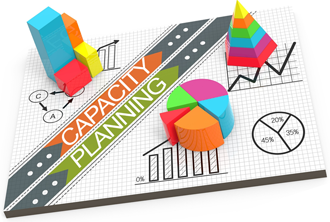



Capacity Planning Meaning Classification And Its Goals



Larry Smith The Manager Of Cases For You Wants To Use Aggregate Planning For The Company S Line Of Rugged Carryon Suitcases Below Is The Company S Course Hero
0 件のコメント:
コメントを投稿